
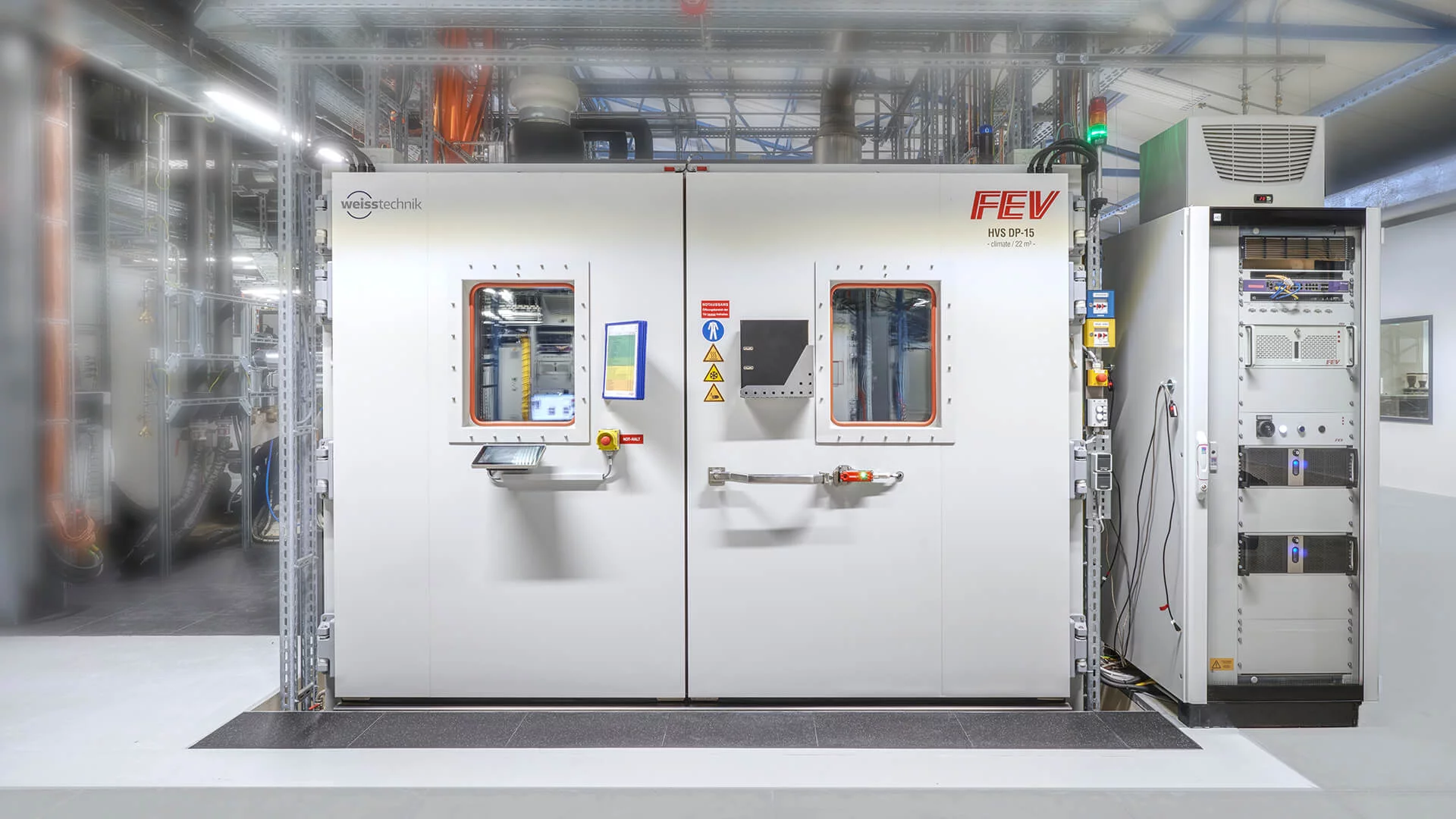
To meet the automotive test standard LV 124, the lithium-ion batteries have to pass a variety of temperature tests.
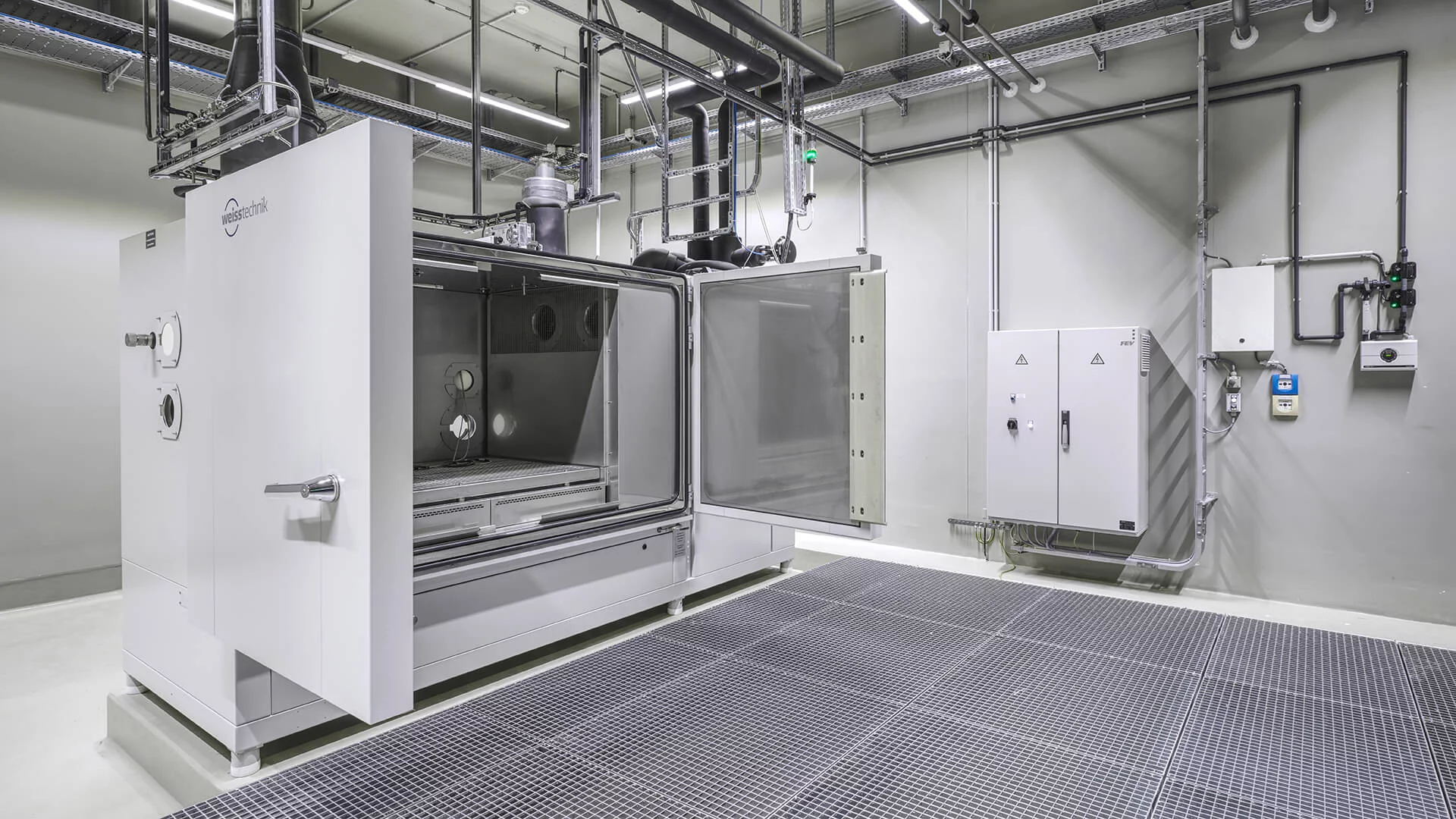
ClimeEvent climatic test chambers were modified according to customer specifications for the diverse climatic tests according to automotive test standard LV 124.
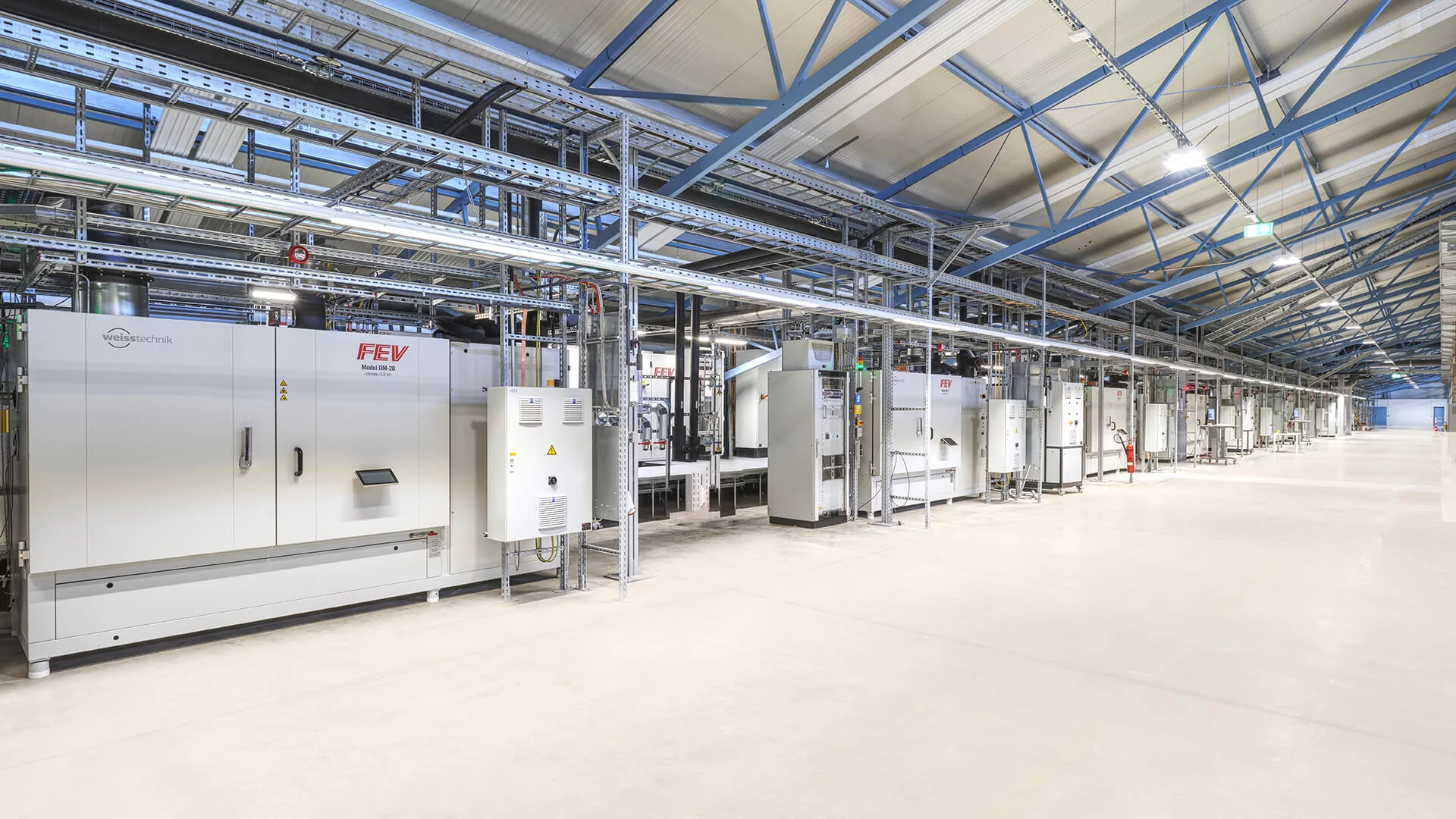
The TempEvent temperature cabinets for testing according to the automotive test standard LV 124 are specially tailored to customer requirements and have open interfaces that can control customer equipment and receive data from it.
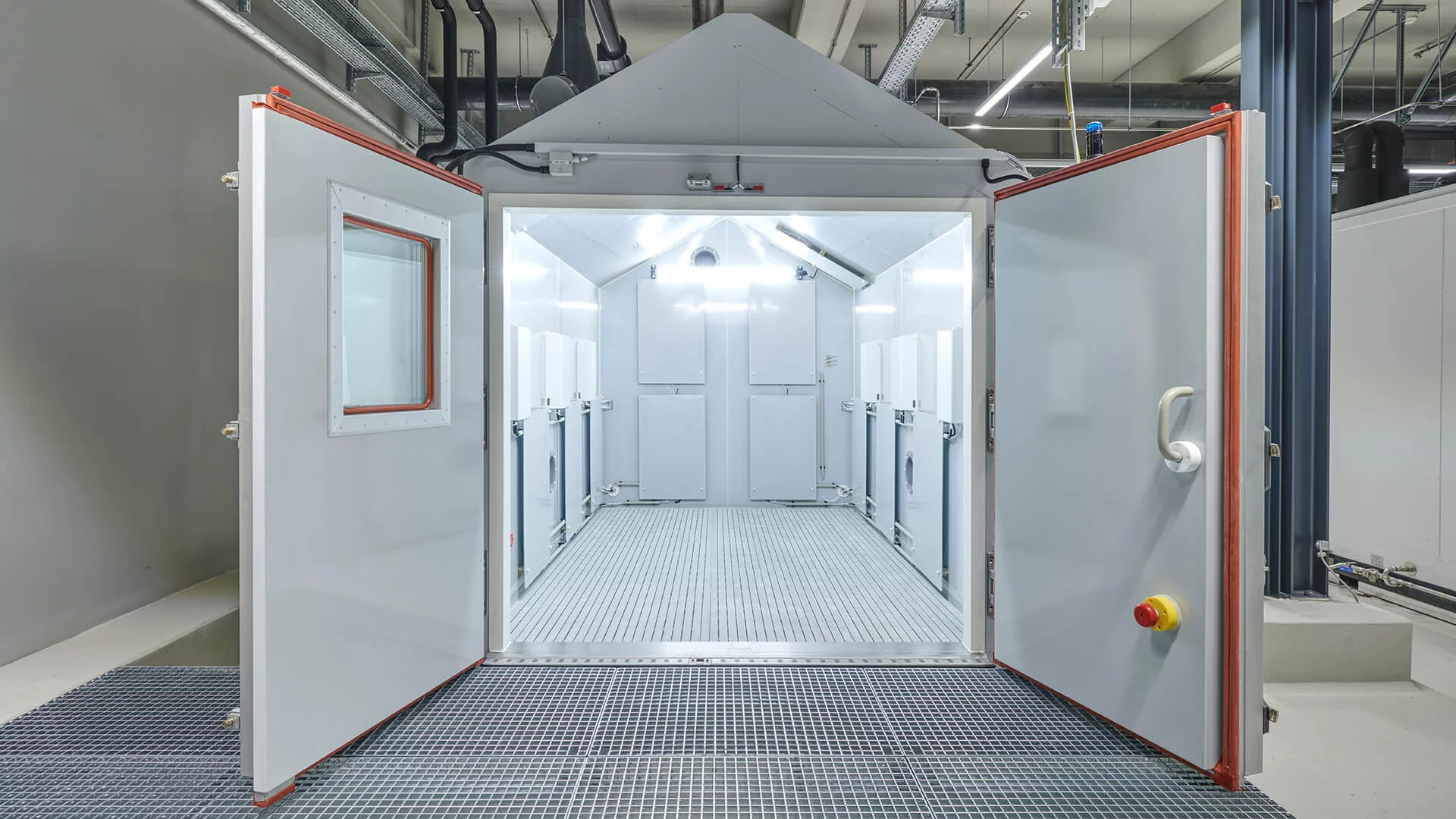
The corrosion resistance of lithium-ion batteries for electric vehicles is tested using salt spray tests.
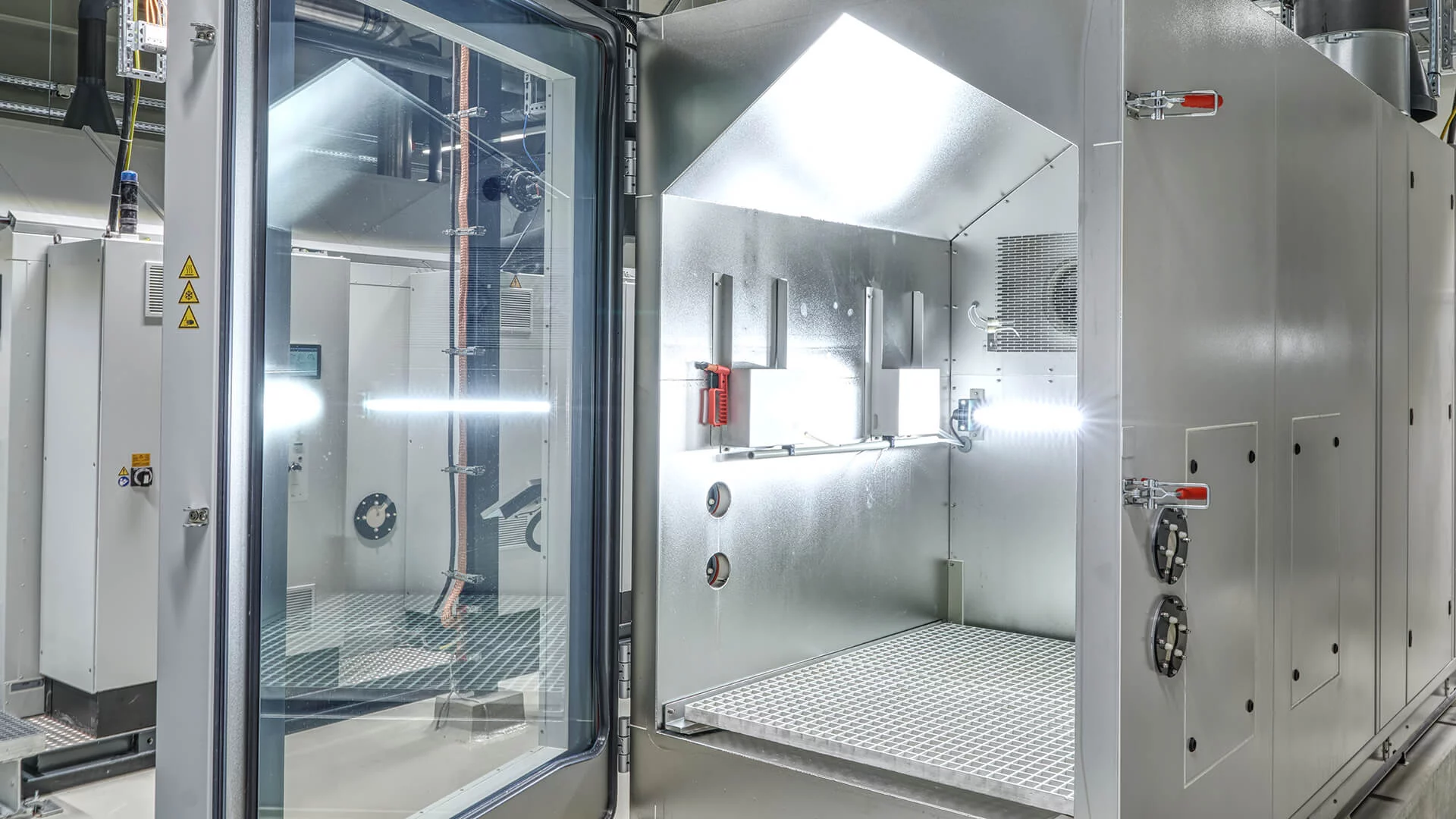
Salt, condensation and changing temperatures - the climate change corrosion test chamber tests lithium-ion batteries under the harshest conditions.
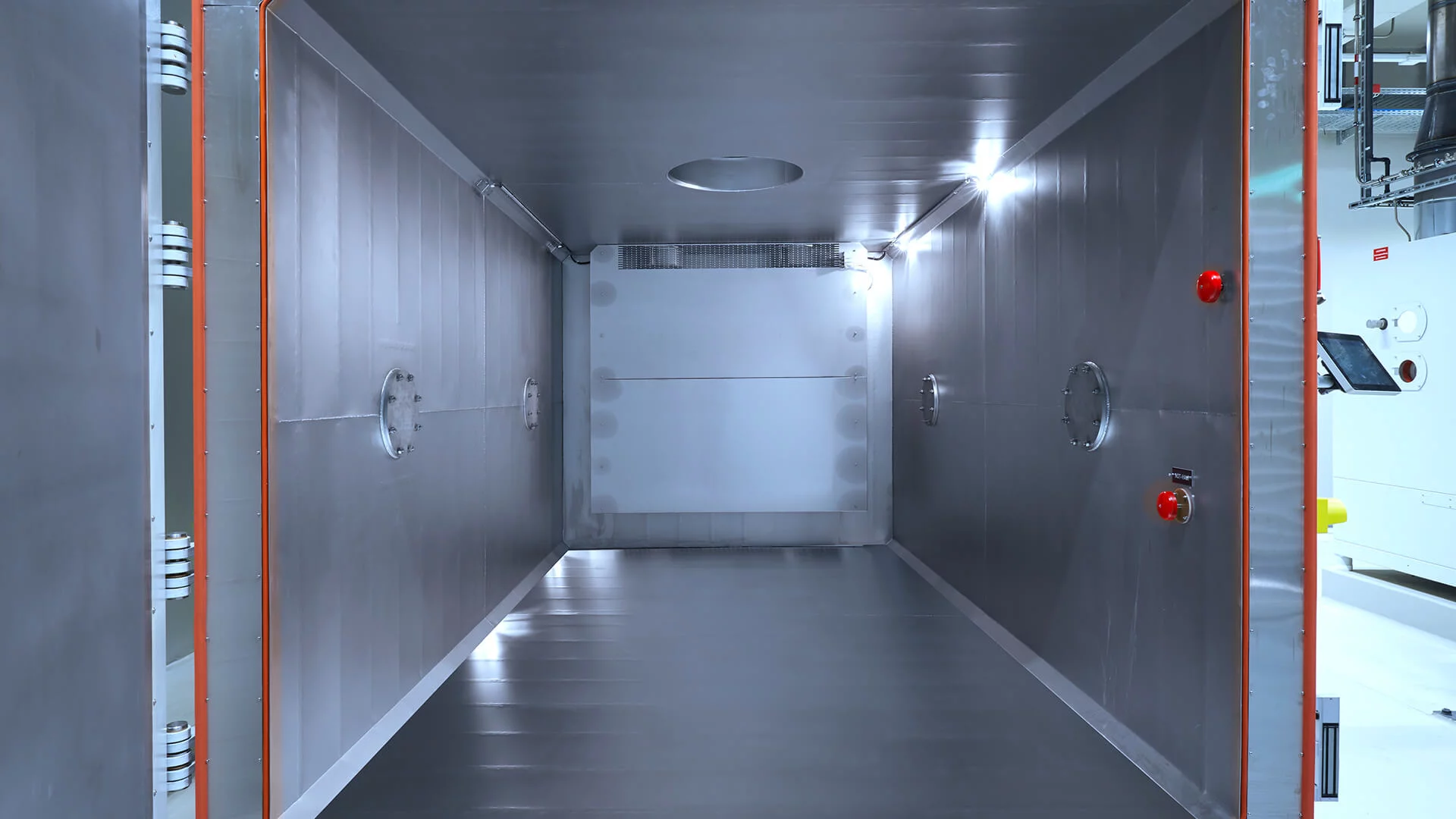
To ensure that lithium-ion batteries can be transported by air, they must be subjected to a negative pressure test.
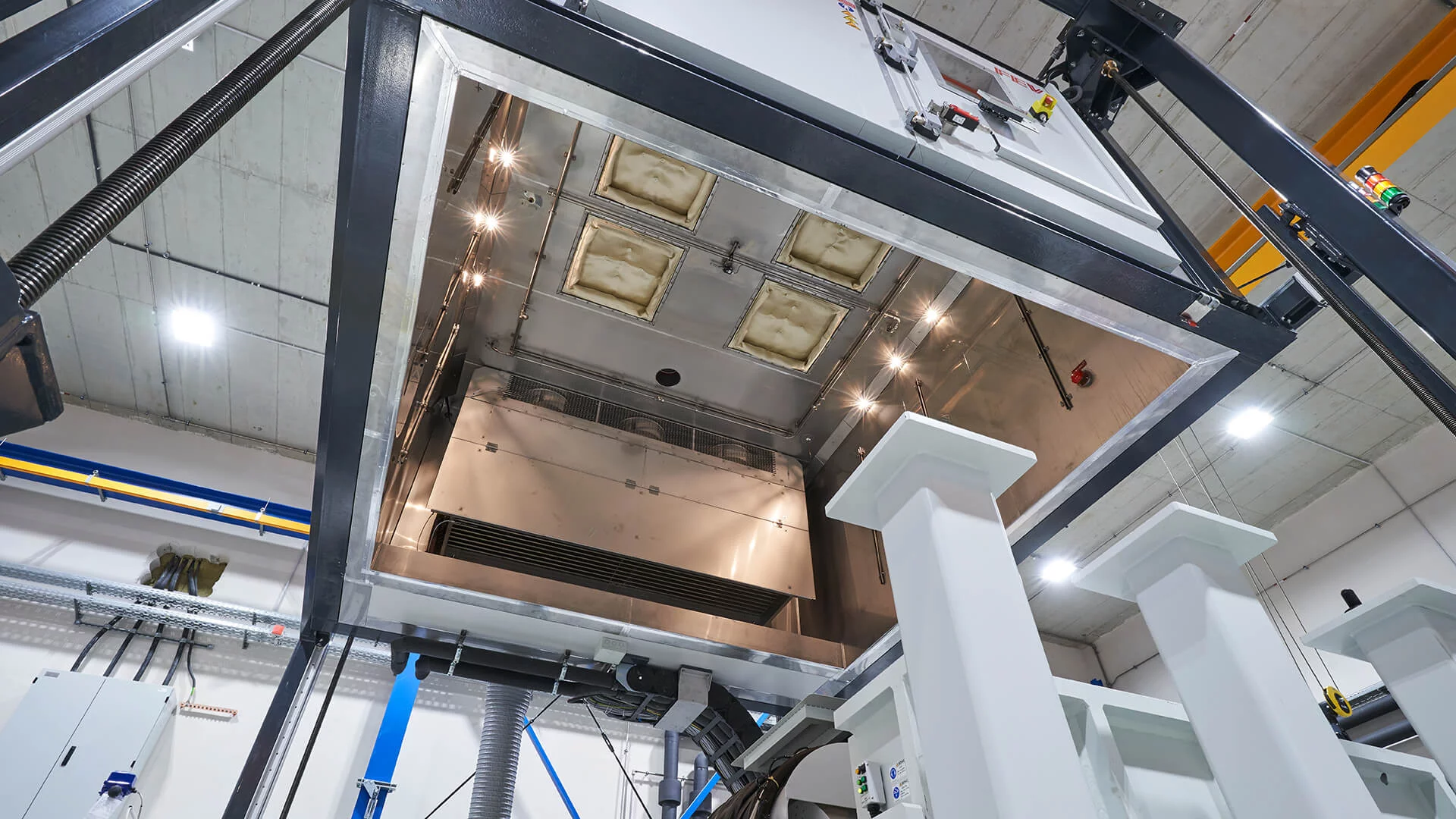
Vibration tests are carried out to investigate the material properties and the function of the energy storage devices in driving operation.
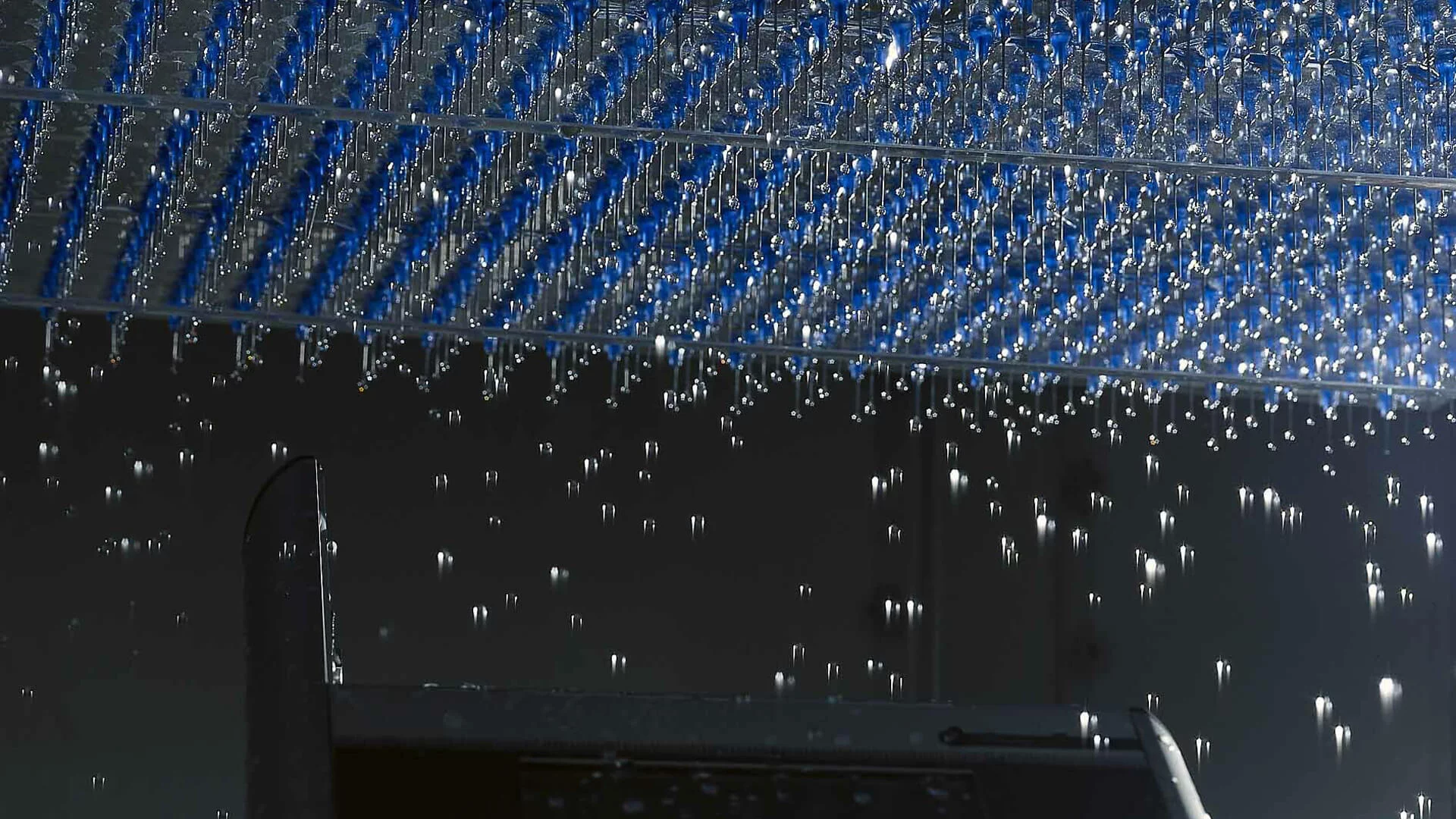
The spray water test checks the tightness of batteries or entire battery packs.
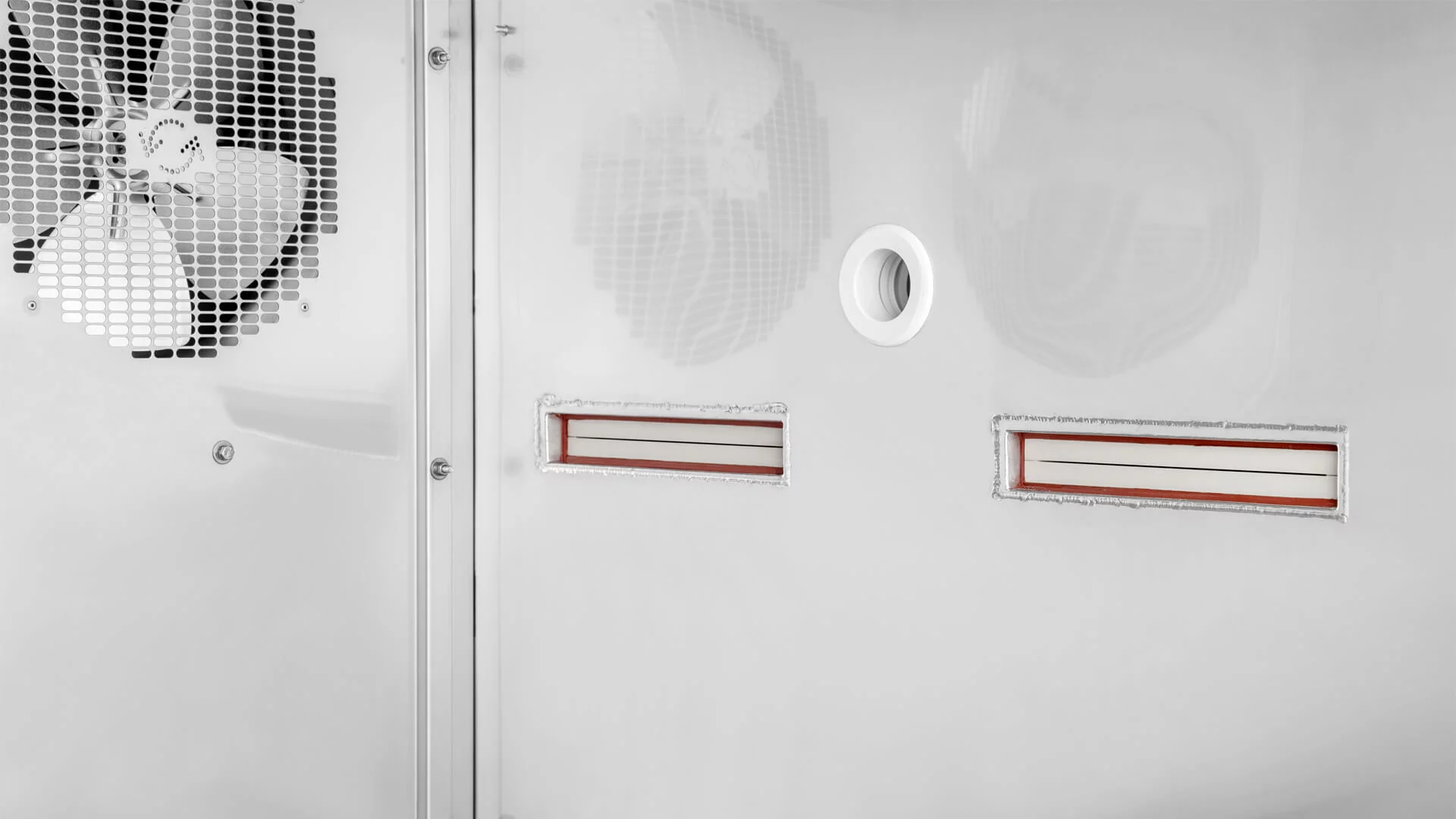
How energy storage units react to a shock-like cooling by cold water is tested in the splash water test.
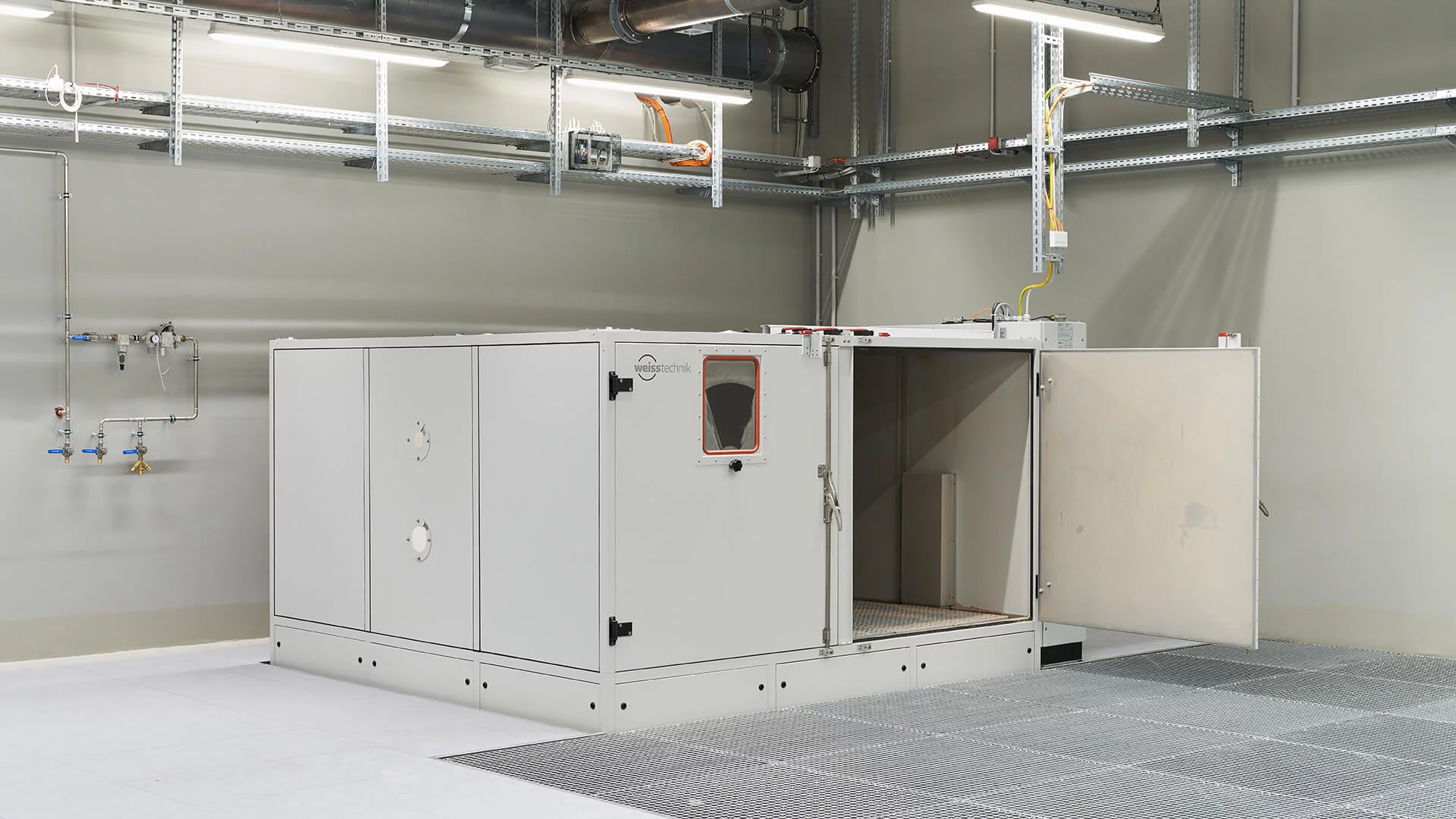
Lithium-ion batteries are subjected to protection type tests to check dust protection and tightness.
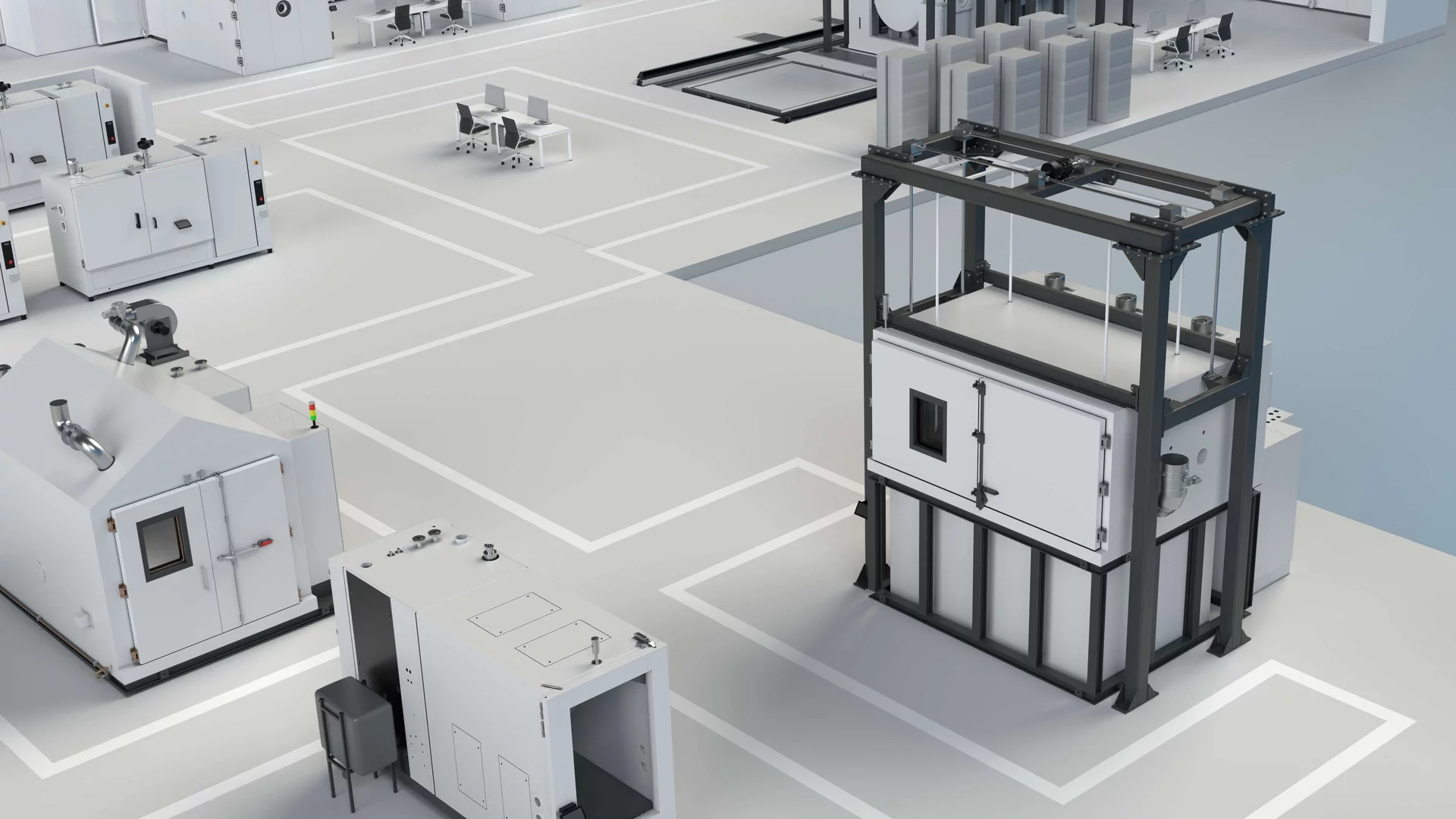
High-voltage batteries for electric vehicles must be tested for their functionality when suddenly immersed in cold water.
DISCOVER OUR TEST RIGS
Heat, cold, humidity, wind and dust: in the world's largest battery test center, energy storage devices undergo a wide variety of environmental simulations.
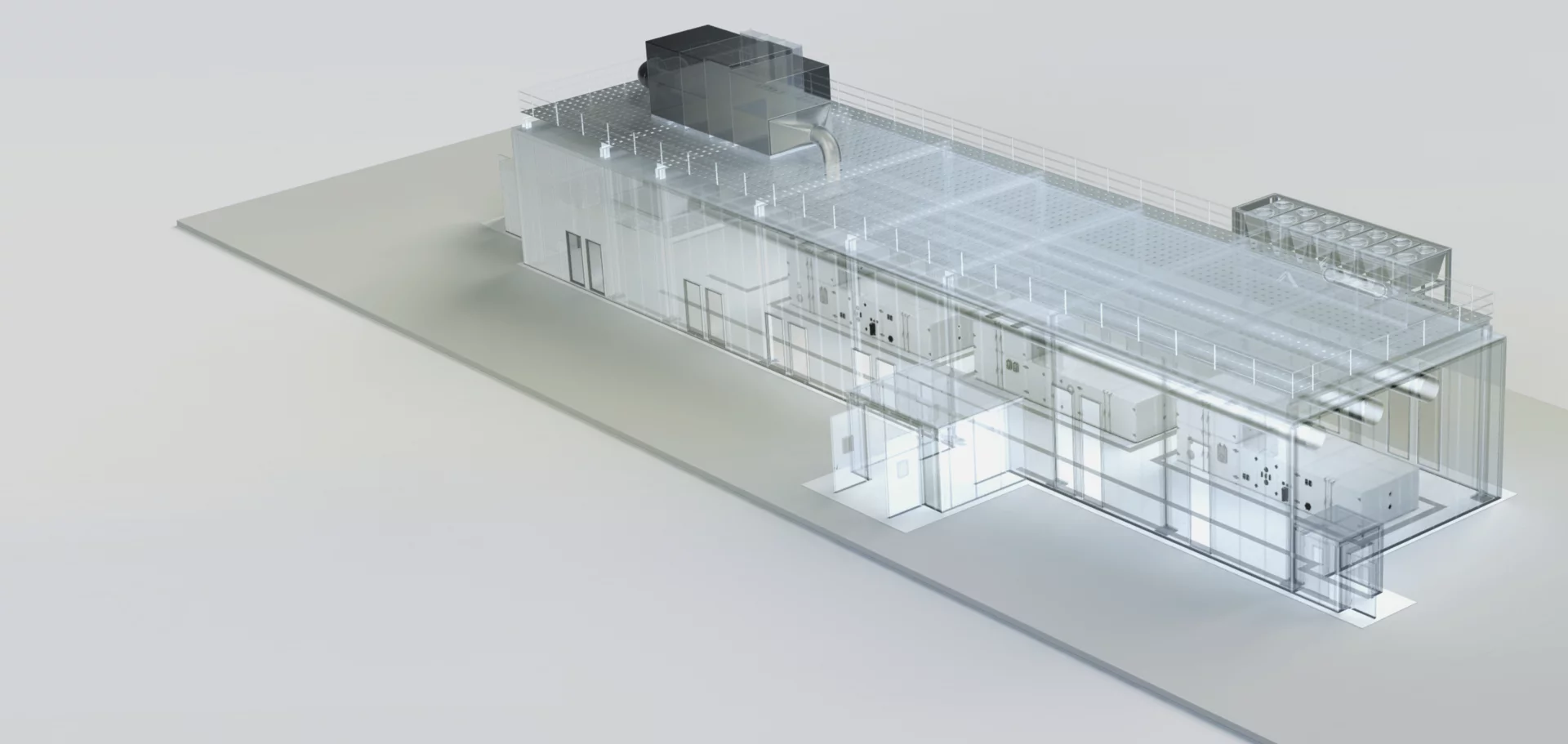
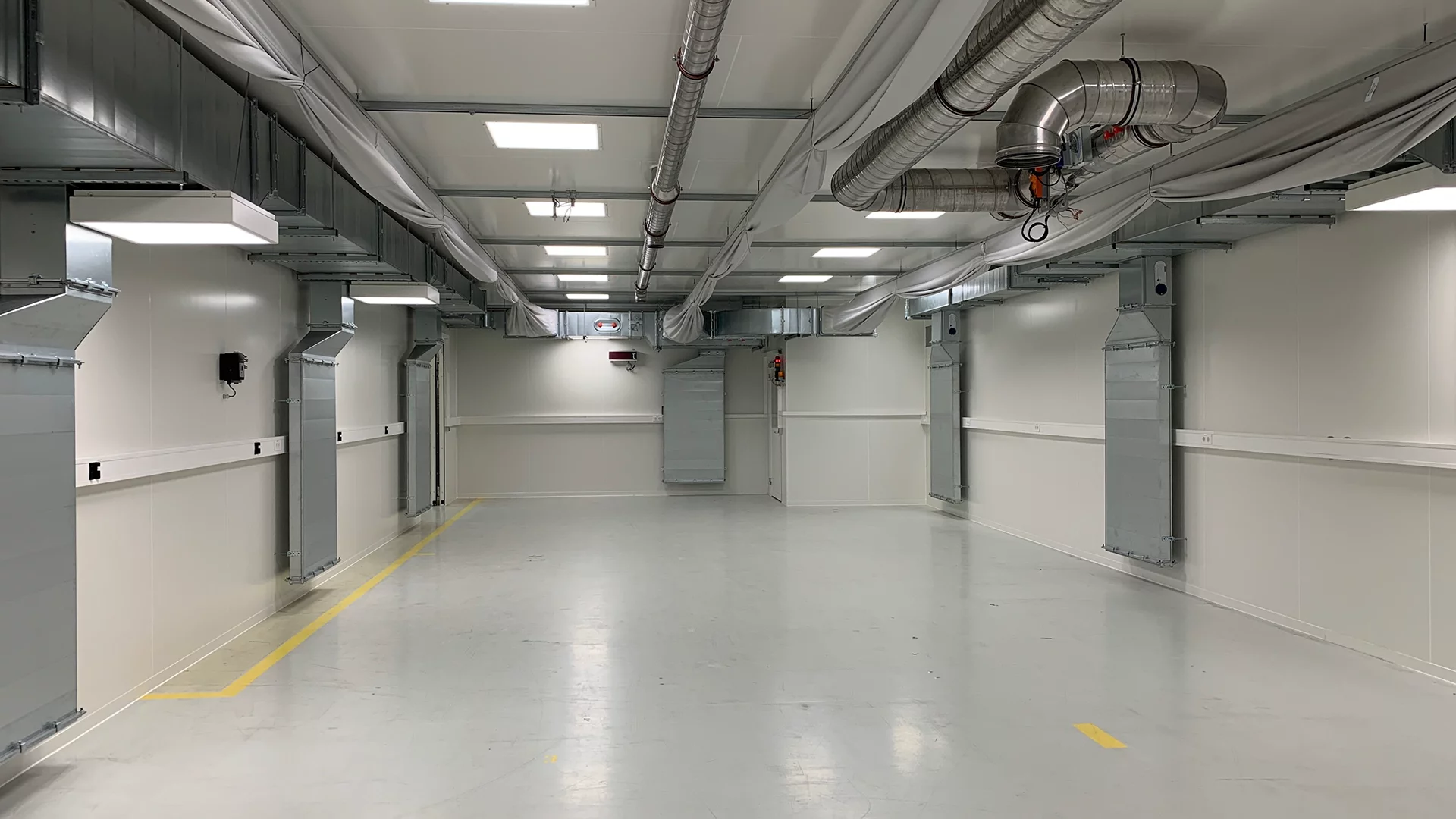
In battery cell production, even a low level of humidity in the end product causes quality losses and even a fire in the battery. A dry room system is therefore indispensable.
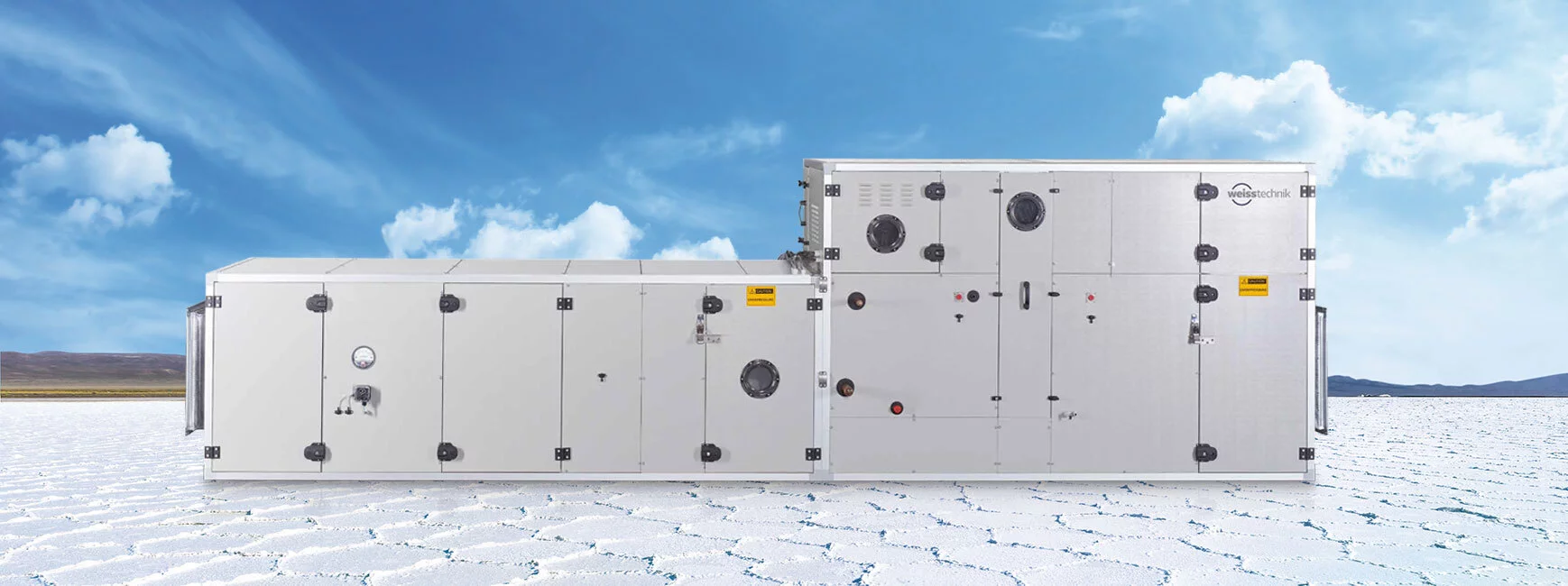
Air dehumidification systems are used for the targeted drying of air flows in industrial processes.
DISCOVER OUR SYSTEMS
In battery cell production, even a low level of humidity in the end product causes quality losses and even a fire in the battery. A dry room system is therefore indispensable.
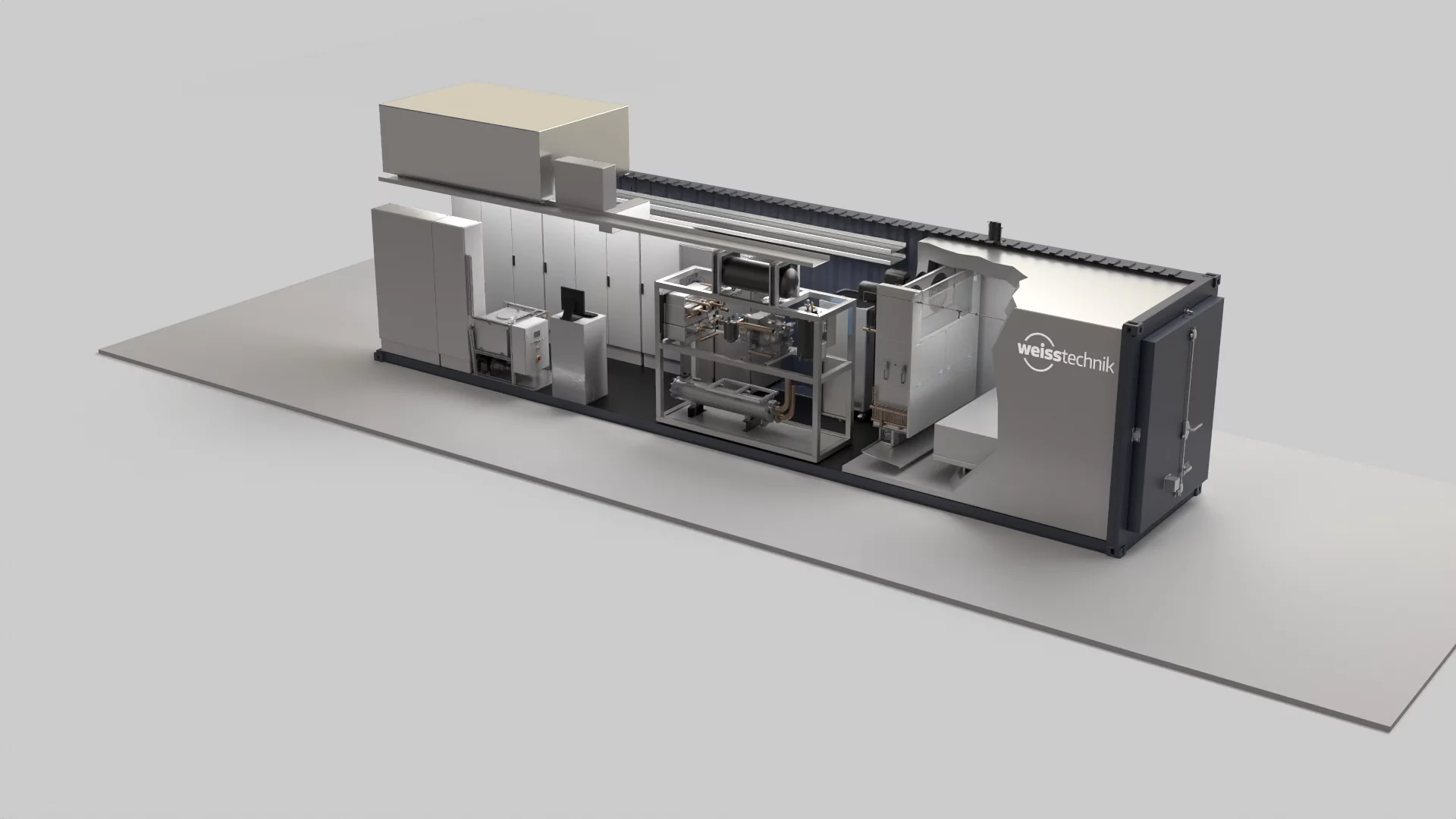

This test chamber has been designed by Weiss Technik for battery testing.

In order to be able to test the test item properly, contacting to the Plug&Test Lab must be individually adapted to the specimen.

The air treatment system ensures homogeneous conditions in the chamber.

The two refrigeration units form a cascade to be able to reach low temperatures quickly.

The user-friendly software is used for central control and regulation of the subsystems in order to be able to create test sequence developments, data evaluations or measurement reports.
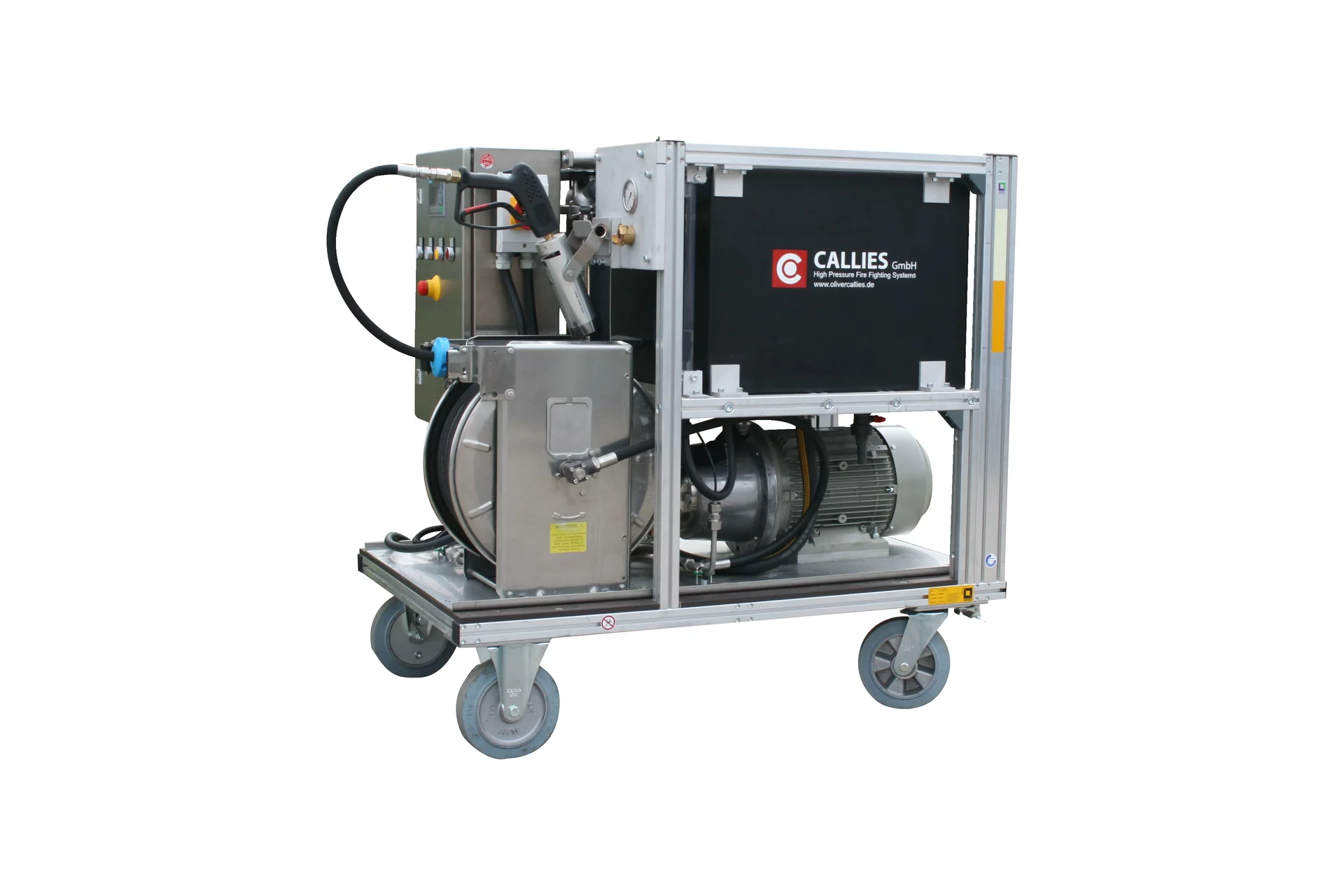
The high-pressure water system protects the climatic chamber from total destruction by battery fire.

All electrical drives and measurement devices for the climate chamber and refrigeration compressors are installed in the switch cabinets to ensure safe operation.

With the help of the chiller mounted on the roof of the climatic chamber, all the waste heat is removed from the container.

The cyclers supply power to the battery under test. Charging processes and driving operation can be shown realistically.

The centralised automation system brings together all the communication paths for automating the test stand.

With the decentralised automation system, the control electronics are connected to a central CPU via a bus system in order to be able to record measurement signals in real time.
Discover the innovative test system for vehicle batteries!
The mobile, container-based Plug&Test solution from Weiss Technik and DSA for standard-compliant temperature and climate tests of lithium-ion vehicle batteries.

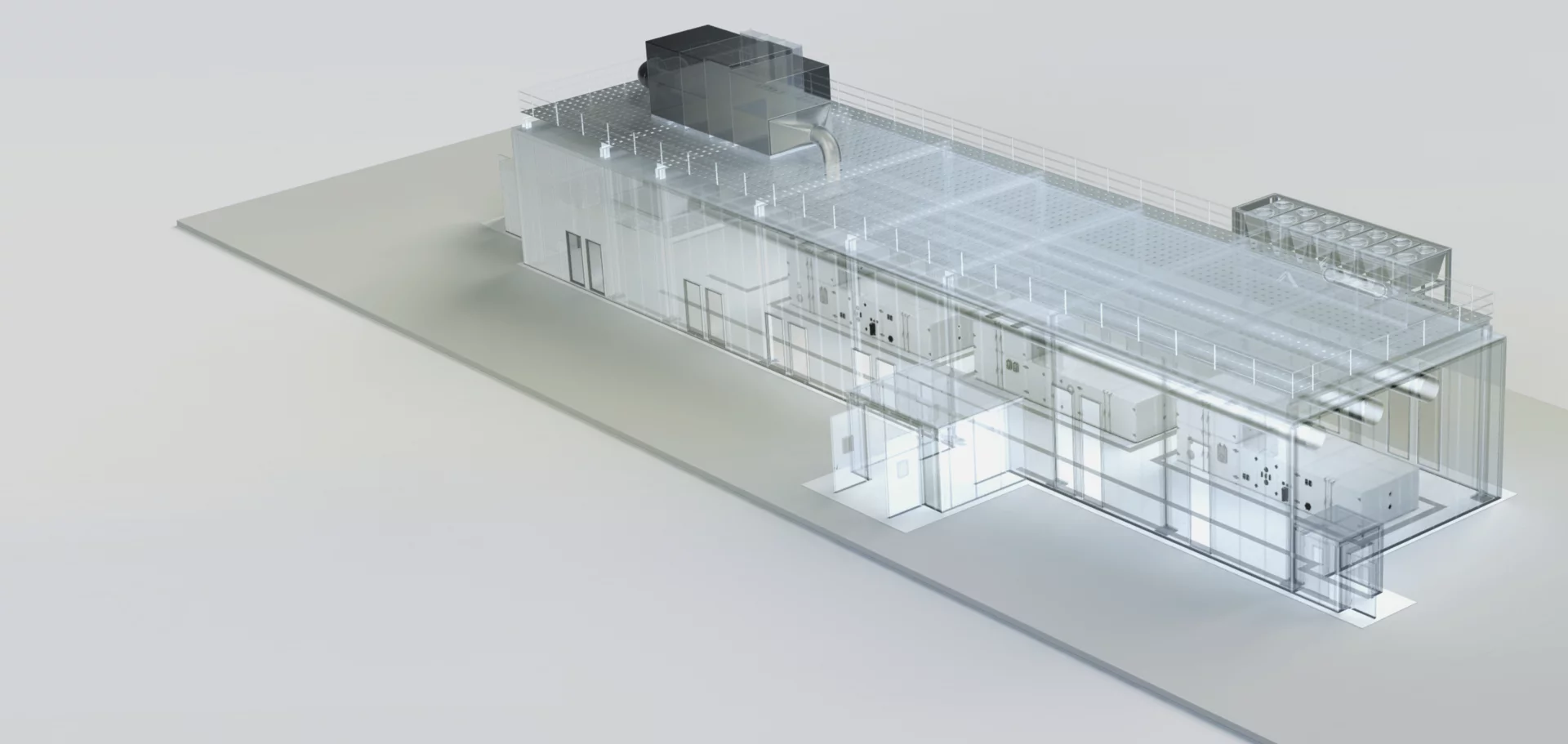
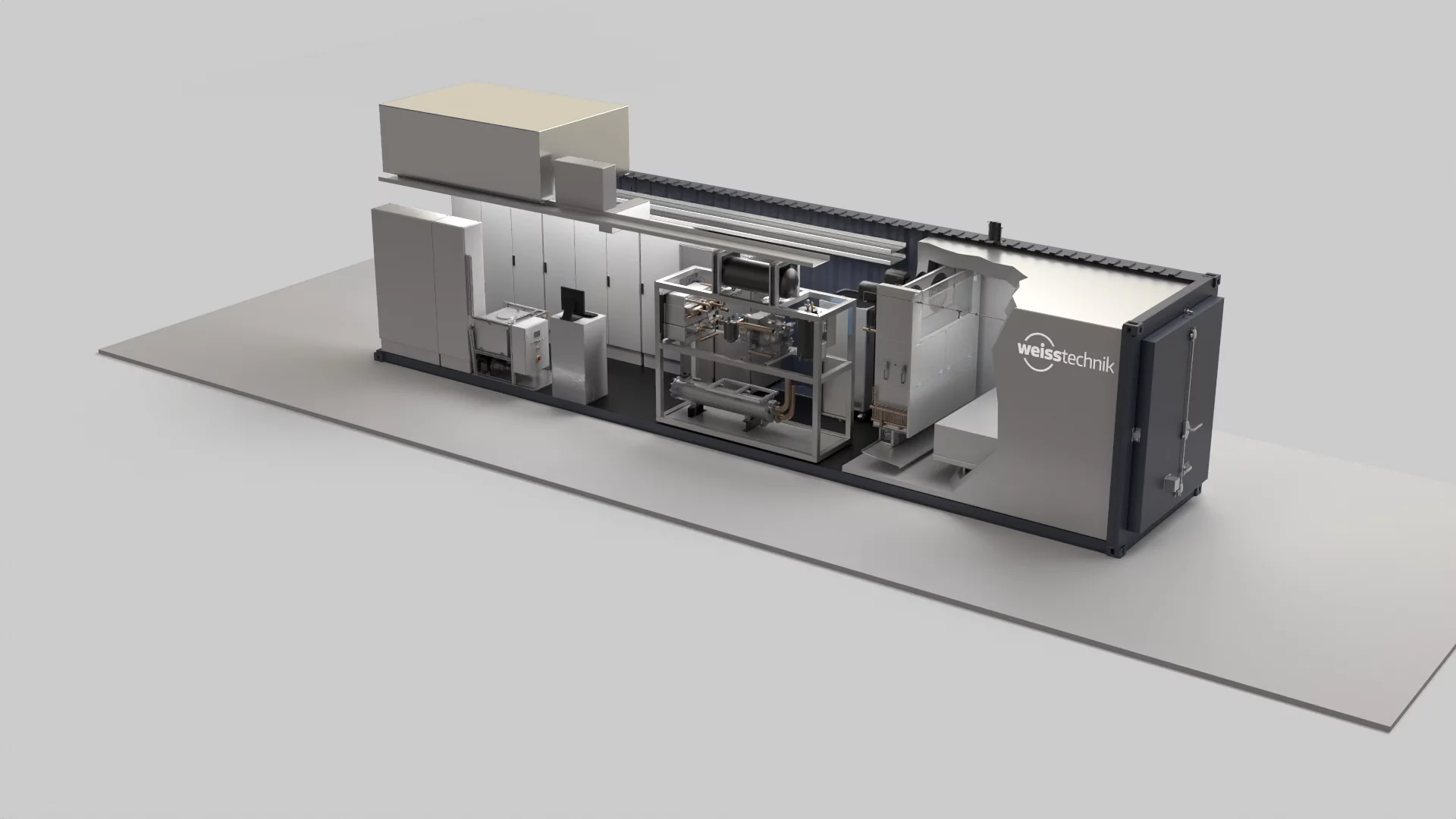