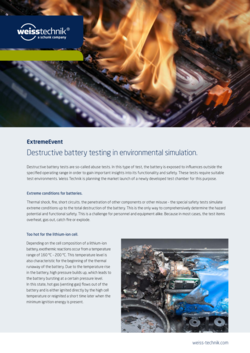
Battery Abuse Testing - Destructive battery testing in environmental simulation
Flyer
Lithium-ion batteries have established themselves as one of the leading energy storage technologies and are widely used in a variety of applications, including portable electronics, electric vehicles, stationary energy storage, and renewable energy systems. A MarketsandMarkets report forecasts that the lithium-ion battery market will be worth $94.4 billion by 2025, growing at about 16.2% annually. Overall, lithium-ion batteries offer many advantages as a powerful and efficient energy source. However, it is important that we are aware that there are also potential hazards associated with their use and handling and that appropriate precautions are taken to minimize these risks.
Certification of lithium-ion batteries is performed by independent organizations that conduct tests to confirm compliance with relevant standards and regulations. These tests typically include tests for thermal stability, shock, vibration, overcharge, short circuit, mechanical penetration or integrity, and other hazards. The tests are performed to ensure that the batteries are safe and do not pose a hazard to the user or the environment.
A number of tests are required for batteries to be placed on the market and used in automotive applications. The test conditions are specified in the relevant norms and standards (national or international). Battery tests are performed at cell, module, pack or vehicle level. Basically, battery testing can be differentiated between performance and aging tests, environmental simulation tests and safety tests.
Safety testing, also known as battery abuse testing, involves exposing the battery to conditions outside the actual operating window. Battery Abuse Tests are destructive safety tests on batteries. An example of a destructive safety test is an overcharge test, in which the battery is charged to a higher voltage than normally recommended. This can cause the battery to overheat and potentially fail or explode. Another test is the so-called "nailing", in which the battery is pierced with a pointed object. This type of test is intended to bring the cells into the event in order to determine how quickly the event spreads to other cells. The nail creates an "internal" short circuit. This is intended to simulate particles that can enter the cell during production and thus short-circuit the electrodes internally in due course.
These so-called battery abuse tests are usually accompanied by a thermal runaway, i.e. fire or explosion. The battery is intentionally overcharged, overheated or damaged to test how it responds to these extreme conditions. The purpose of this type of test is to examine the behavior of the battery under extreme stress to ensure that it is safe, reliable, and poses no hazards. Especially in applications where they can cause potentially dangerous situations, such as in electric vehicles or portable electronic devices. Destructive tests can minimize the risk of accidents and fires, ensuring greater safety and reliability. They are also a prerequisite for the marketing and development of new batteries.
Environmental regulations and an increasing awareness of occupational safety prevent tests in open environments or old, empty dwellings (bunkers, hangars) without subsequent exhaust gas treatment. Thus, they cannot be part of a professional test concept with reproducible environmental conditions.
A lithium-ion battery is generally operated safely in the range up to 100°C without any lasting effects. If the temperature level rises above this, corresponding decomposition reactions begin inside the battery. Above a temperature of approx. 120 °C, the so-called solid electrolyte interphase (SEI) first decomposes and, a little later, the separator material between the anode and cathode gradually dissolves. Depending on the cell composition of a battery, exothermic reactions occur from a temperature range of 160°C ... 200°C. This temperature level is also characteristic for the beginning of the thermal runaway of the battery. In the case of lithium-ion batteries, reaching this state depends primarily on the type of cell failure (misuse condition) and the cell composition, as this has a significant influence on the rate of temperature rise within the battery cell.
At a temperature rise of 10 K/s, thermal runaway is assumed. When this condition is reached, uncontrollable heat release can no longer be prevented, i.e. the heat generated can no longer be dissipated to a sufficient extent. The resulting heat energy causes the exothermic reactions to continue to accelerate. Due to the temperature increase in the battery, a high pressure builds up, which, above a certain pressure level, causes the battery to burst. In this condition, hot gas (venting gas) flows out of the battery and is either ignited directly by the high cell temperature or re-ignited a short time later when the minimum ignition energy is present. Since one reaction product in the decomposition reactions is oxygen, among others, the combustion process is maintained. Therefore, only the effects of the fire can be contained. It is not possible to extinguish the fire completely.
1. Mechanical testing | |
In the mechanical tests, an object penetrates or traverses the battery (mechanical integrity). For example, the extent to which nail penetration (internal short circuit) or crushing (crash) affects the functionality and safety-related behavior of the battery is examined. | |
2. Thermal testing | |
During the thermal tests, the batteries are subjected to ambient low to excess temperatures, with the excess temperature tests in particular leading to thermal runaway in most cases. Here, the surrounding air is heated up to 200°C or even higher, which raises the battery to a critical temperature level after a certain time due to heat transfer processes. | |
3. Electrical testing | |
During the electrical tests, various critical scenarios are tested that may exist in connection with the surrounding electrical periphery. For example, a short circuit is generated (external short circuit) or the battery is deliberately overcharged at a higher voltage level. As a result, the battery heats up and also quickly enters a critical state. |
In order to determine an adequate test system, it is decisive what kind of tests are carried out and what effects are to be expected from the battery test specimen during the test. From this, the hazard potential is derived, which varies from "no hazard" to an explosion with harmful gases.