Thermal treatment of plastics
Obtain easily-reproducible results
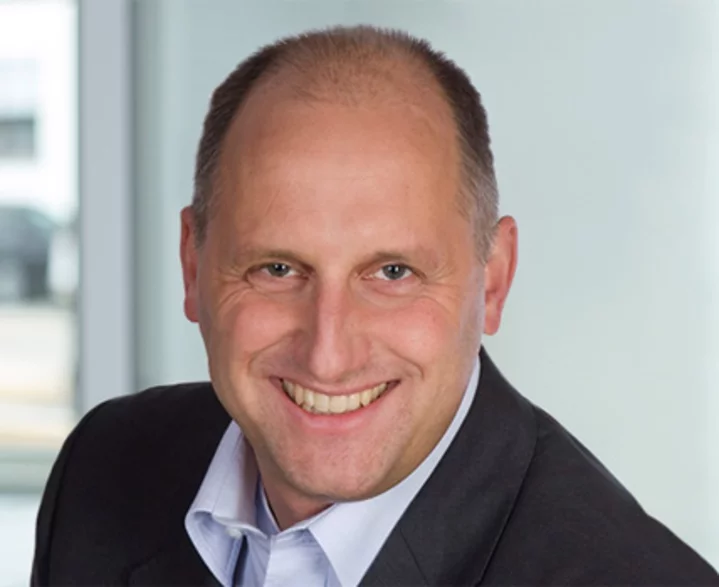
Ask an expert
Interview with Stefan Betz, Product Manager Heat Technology
Why do plastics undergo thermal treatment?
Today, more and more products are made using one or several types of plastic. At the same time, customers are becoming increasingly demanding in terms of the desired properties, uniformity and longevity of products. Our heat technology enables manufacturers to always create exactly the same processing and production conditions, in order to reliably achieve constant product quality.
Which areas is heat technology used in?
The scope of application of our industrial ovens is virtually unlimited. They are used, for example, for the crosslinking of elastomers and the tempering or curing of silicone elastomers. They are also used to heat plastics to improve their shaping or thermosetting properties. Other areas of application include the drying and curing of coatings or fibre composites, as well as the sintering of PTFE, and the polymerisation of contact lenses and plastic lenses.
What are the current development trends?
The e-mobility sector is an increasingly important business segment for us. Our ovens are used for bonding stator packs for electric motors. The medical technology sector is also promising. Our ovens are used for manufacturing implants, prostheses and stents, as well as for coating medical equipment. We also serve several customers in the automotive and aerospace sectors, as well as in the electronics and pharmaceuticals industries.
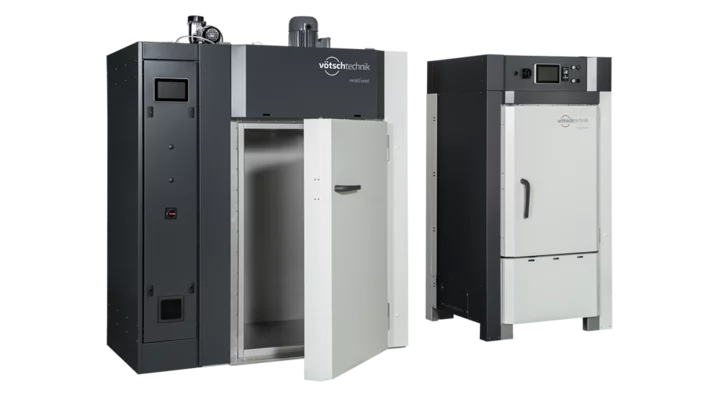
Industrial thermal technology
Easily-reproducible conditions
The company is a leading global specialist in industrial heat technology, and a partner to many businesses in the plastics industry. Our process-optimised industrial ovens suitable for specific materials are designed for industrial use. Thanks to particularly homogeneous temperature distribution and conditions which are reproducible at any time, they ensure constant process conditions and therefore consistent product quality with the same physical properties.
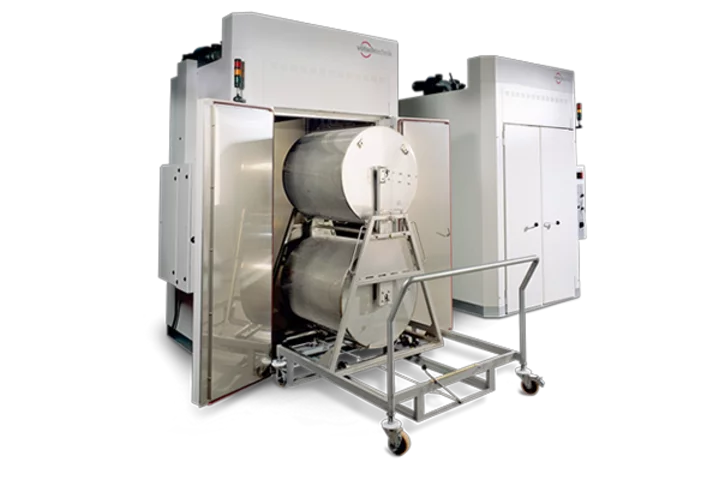
Standard hot air ovens
Versatile, reliable, tried-and-tested
Our hot air solutions are typically used as chamber ovens for tempering silicone elastomers. Depending on the requirements, these can be equipped with a greater supply of fresh air, increased tightness, or a loading ramp for easy loading and unloading. Smaller products and bulk materials can be tempered in a rotary drum.
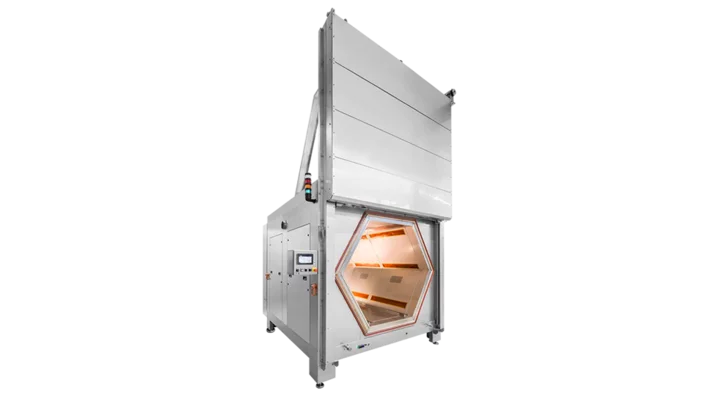
Efficient microwave ovens
Uniform, economical, quick
As well as standard hot air ovens, we offer microwave ovens for industrial heating and drying processes. These ensure a particularly high degree of field uniformity and a reduced energy requirement with minimised heating and cooling times. The heat is transferred without any losses, and penetrates deep into the product.
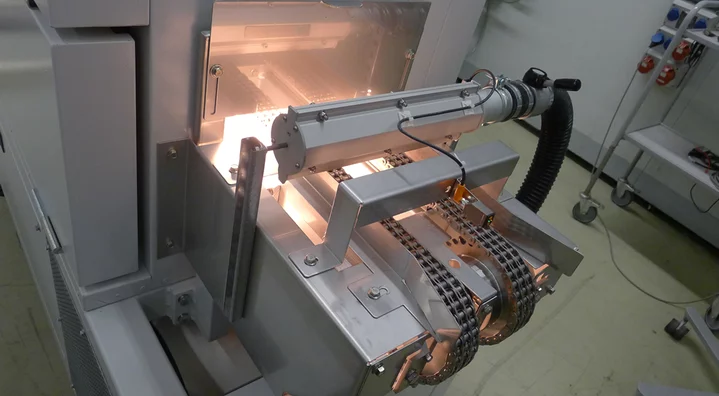
Versatile infra-red ovens
Flexible, efficient, quick
Our infra-red solutions are suitable for a wide variety of industrial production steps. They heat up quickly, evenly and energy-efficiently, and can be combined with heat if required, or used in a mobile drying oven. We provide customised infra-red ovens, infra-red modules, and infra-red emitters.
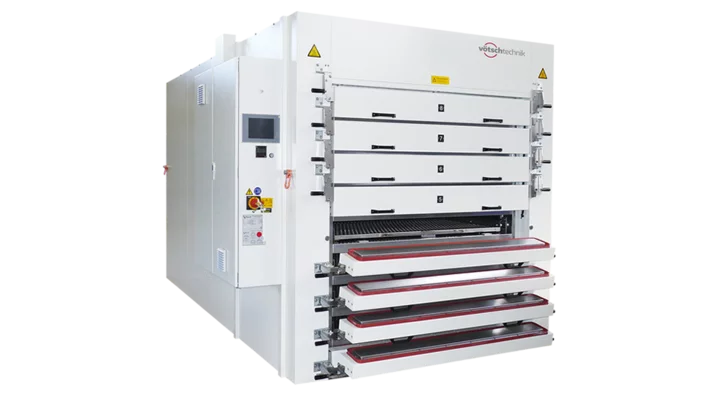
Batch process
Using flexible means
We develop and produce high-performance ovens, which are well-equipped in the basic model, for batch processes. These ensure a small carbon footprint and can be equipped with drawers, retractable trolleys or rotary drums, according to the product and requirements.
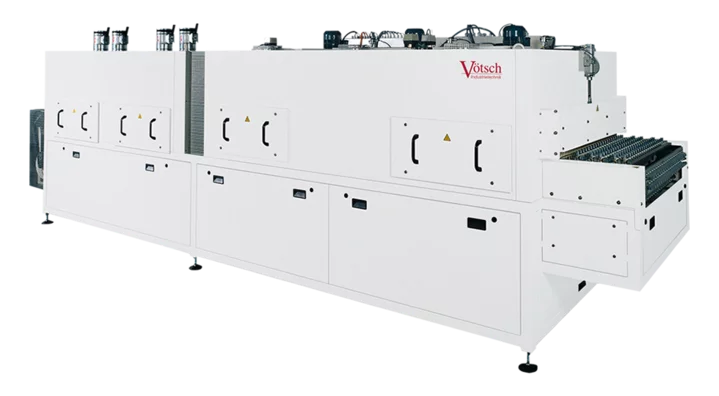
Continuous production
Simple, economical production
Our conveyor ovens are reliable building blocks for highly efficient production lines. They can either be flexibly assembled from standard modules or designed and constructed in a customised manner. The air flow can be horizontal, vertical or double-sided. A range of variants are possible in the conveyor system.
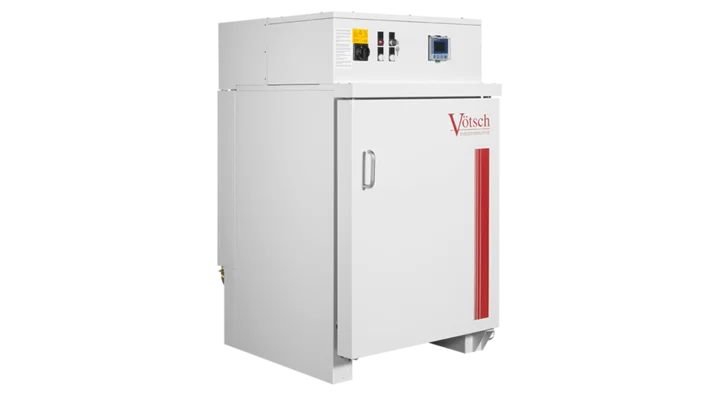
Numerous special solutions
Explosion protection, fire protection, clean room
If flammable or explosive fission products (peroxides above 80°C and siloxanes above 150°C) are released during the process, we offer our customers safe extensions. This also applies to hygienic clean room designs up to class ISO 7, used for example in the medical and food industries (FDA, BfR).