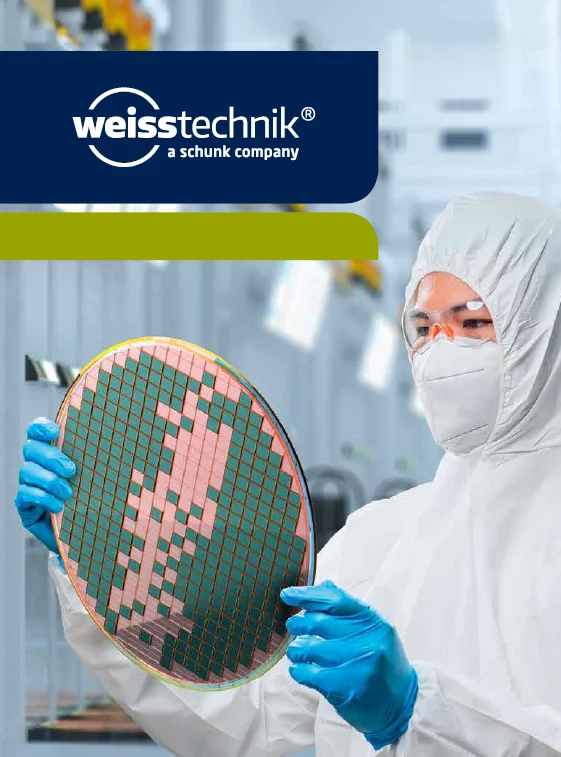
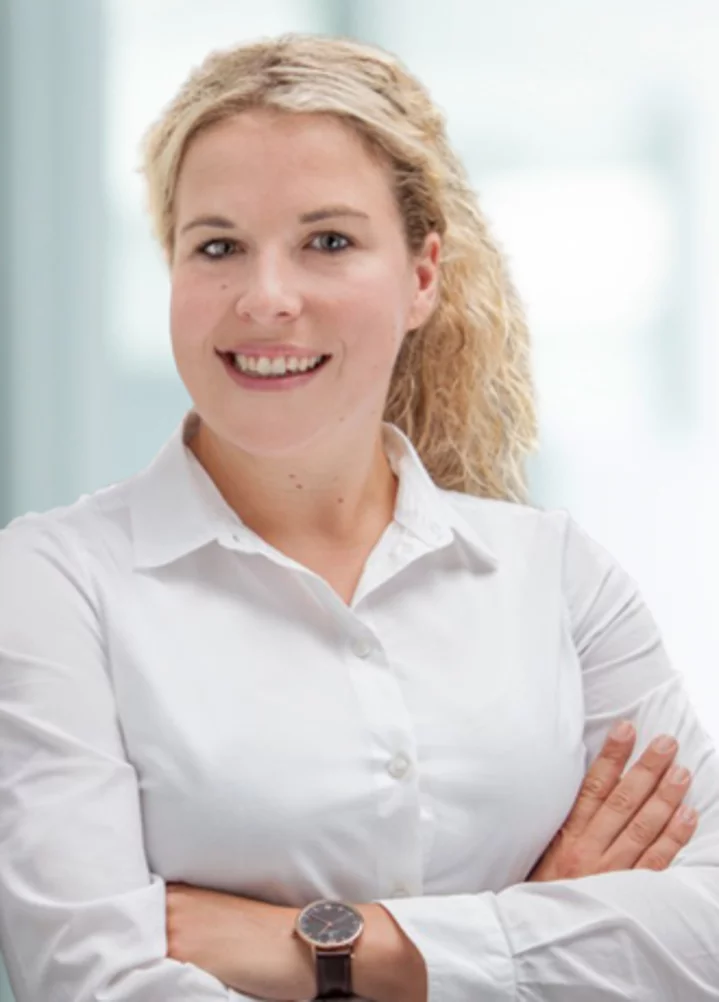
Interview with the expert
Sabrina Radoske
Sales Manager Ophthalmic & Microelectronics
What is so special about semiconductor production?
The production of semiconductors is a lengthy, complex and highly sensitive process with high demands on purity and uniformity. To avoid defects in quality, the absence of silicone in the front and back ends is mandatory in many processing steps. As production facilities continue to grow, so does the need for solutions to automate operations. It is therefore important to have all the parameters at your fingertips and to exchange data securely via the SECS/GEM interfaces.
Where and how does Weiss Technik provide support for semiconductor production?
As an experienced specialist in high quality industrial ovens, we design systems that can be used in a variety of processes. In the front end, vötschovens can be used for glass soldering, known as glass-frit bonding, under clean room conditions. They can also be used for end-of-line tests and for drying machine components and wafer shipping boxes. Our systems comply with clean room conditions up to ISO 4.
What advantages does Weiss Technik offer users?
Our many years of cleanroom and industrial experience is important as well as our extensive expertise in the field of thermal engineering. Weiss Technik is also able to draw on its extensive experience in the integration of automated processes and systems. The global service network with competent technicians, standardised processes and short response times is also important to many customers. Another strength of Weiss Technik is the development of individual solutions based on proven technology concepts.
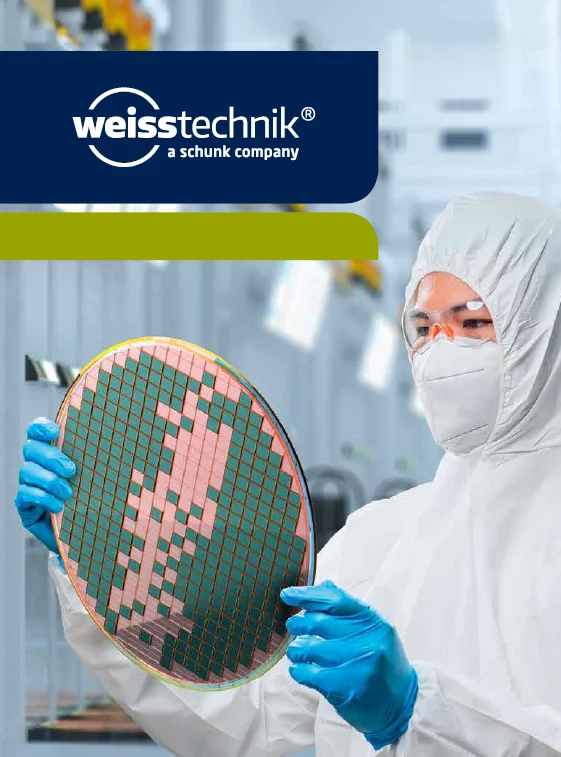
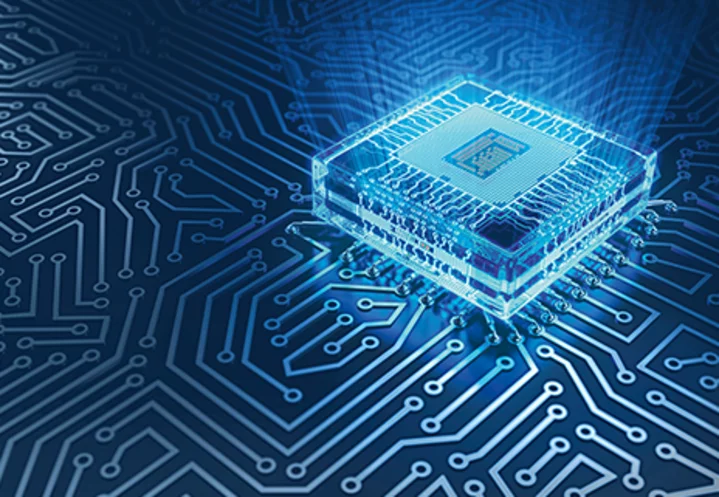
Thermal processing with vötschoven
Reliable, economical, flexible
We implement customised, process-integrated solutions for demanding process steps in the field of industrial heating. Semiconductor manufacturers benefit from our many years of cleanroom experience and our expertise as a specialist in meeting complex requirements.
Advantages
- Customised systems
- Reproducible processes
- Worldwide round the clock service
- Everything from a single source
Find out more about cleanrooms in the semiconductor production.
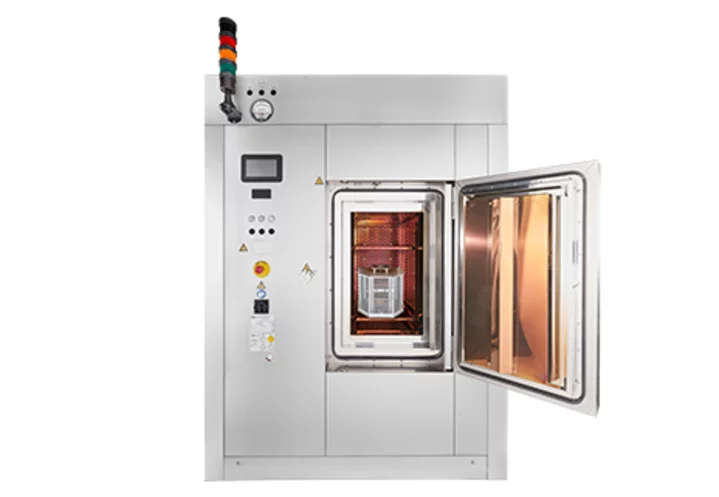
Clean room oven for front end
450°C, compact, silicone-free
To seal MEMS wafers with glass paste, they are processed in an oven with filtered fresh air. The fast start-up of the process ramps and the ideal air flow contribute to the required product quality. The oven has been specifically designed for glass paste to EN 1539, so that the flammable components are expelled in the oven. VTF clean room ovens can be ordered with wall mounting option. The control box can be extended into the grey room to optimise the cleanroom floor space.
Advantages
- Special ovens for glass frit bonding
- Minimum temperature variation (440°C at ±2K)
- Perfect for cleanrooms due to its small footprint
- Integration into the clean room wall
- Silicone-free at 440°C
- SECS/GEM interface
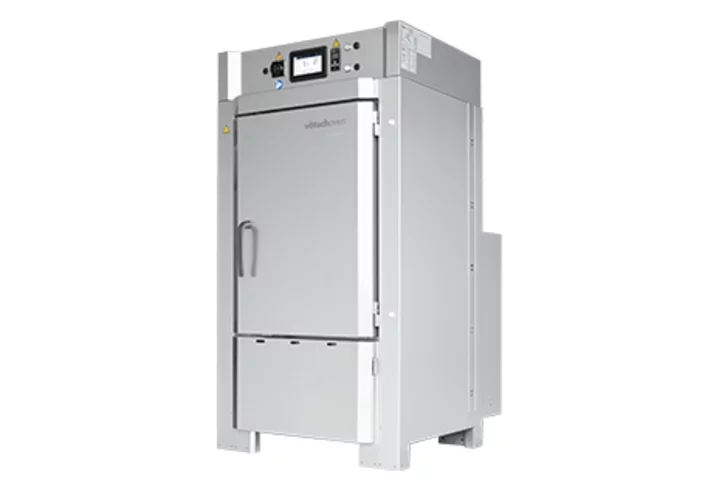
Clean room oven for end-of-line testing
350°C, automated and highly flexible
Ovens for 100% end-of-line testing, such as the Data Retention Bake Test, are used in the transition between front-end and back-end and must operate without silicone. They are suitable for temperatures up to 350°C and operate with various Protective gas or filtered fresh air. They meet the cleanliness requirements of ISO class 7 to 5 and can be loaded manually or automatically.
Advantages
- Flexible air routing
- Fresh air, inert gas or hybrid oven
- Cleanliness ISO 7 to ISO 5
- Completely silicone-free design
- Cooled seals if required
- For ceiling transport system OHT or AGV
- Also available with manual loading as an alternative
- SECS/GEM interface
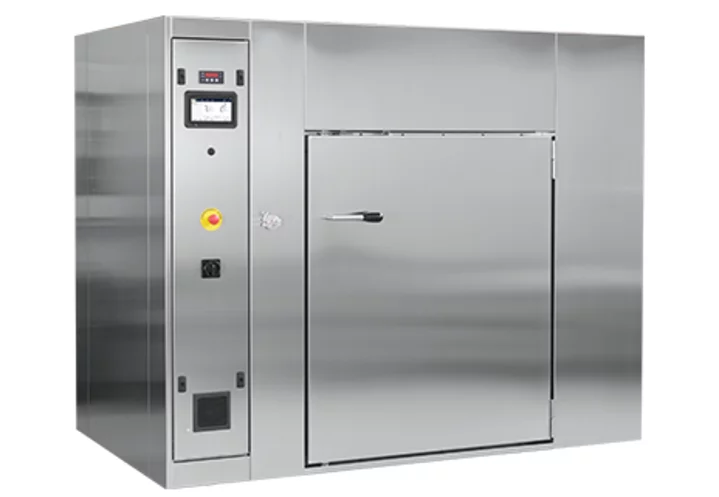
Clean room ovens for drying
For components and wafer shipping boxes
Clean and dry conditions are extremely important for machine parts used in front-end equipment. Therefore, the cleaning and drying of components and shipping boxes play a decisive role in product quality. The space-saving vötschoven cleanroom ovens do this reliably, energy-efficiently and as required.
Advantages:
- Clean drying ovens, up to 180 degrees
- For large applications and numerous components
- Can be used in clean rooms up to ISO 4
- Integrated humidity sensors
- Side-by-side installation possible
- Optional pass-through function
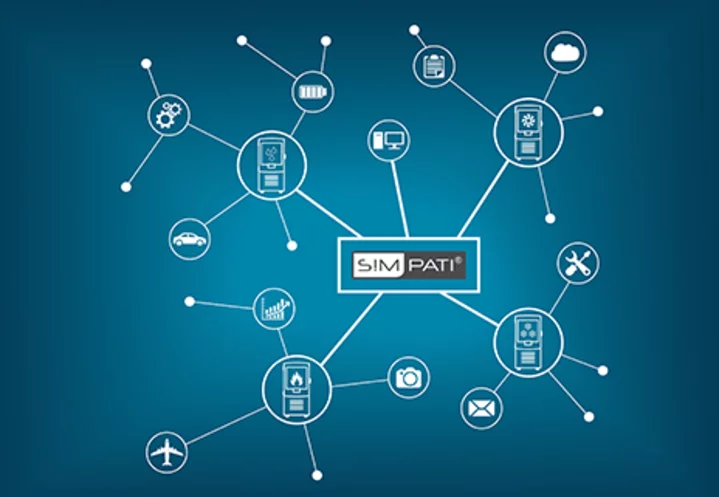
SECS/GEM interface
Easy to integrate
Traceability of each batch and process step is essential for quality assurance in semiconductor manufacturing. The enormous amount of data generated by the numerous process steps is exchanged via SECS/GEM interfaces. vötschoven systems are equipped with the in-house S!MPAC control system and S!MPATI software, which can be extended by an SECS/GEM interface.
Advantages:
- Perfect integration of the ovens into the customer network
- Standard interface for wafer production
- Customised interface for manual processes with barcode or automated 300 mm processes
Interested?
Contact us!
If you would like to learn more about our thermal processing solutions for the semiconductor industry, we will be happy to advise you personally and develop an individual solution for your requirement.