Vakuumtrocknung in der Batteriezellen-Produktion
Prozesssichere Lösungen für effiziente E-Mobilität
Bei der Fertigung von Lithium-Ionen-Batterien ist die Vakuum-Trockentechnik unverzichtbar. Wir projektieren kundenspezifisch abgestimmte Vakuumtrockner, die sich bedarfsgerecht in Fertigungslinien und Forschungsanlagen einbinden lassen. Unsere Vakuumtrockner arbeiten dabei äußerst effizient und prozessoptimiert.
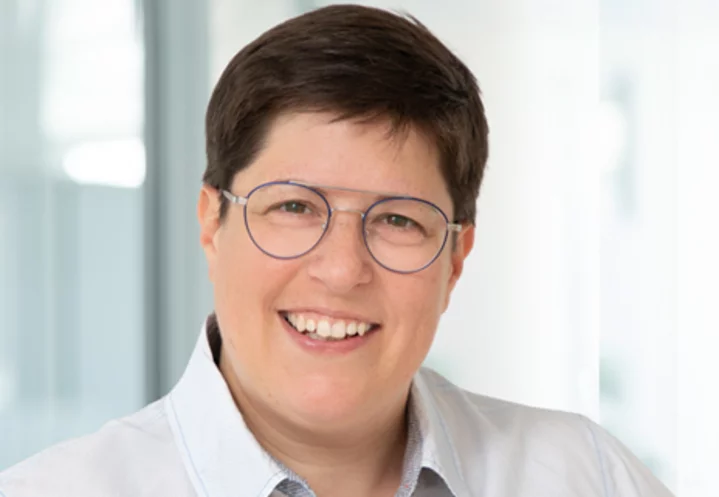
Interview mit der Expertin
Katharina Mayer
Application Manager E-Mobility
Welche Vorteile bietet Vakuumtechnik bei Trocknungsprozessen?
Durch einen reduzierten Luftdruck verringert sich gemäß der Dampfdruck-Temperatur-Kurve auch der Siedepunkt von flüssigen Stoffgemischen. Diese verdampfen dann schon bei deutlich niedrigeren Temperaturen und können aktiv aus einem Rezipienten gesaugt werden. Deshalb müssen sensible Produkte im Vakuum nicht so stark erhitzt werden, um die gleiche Trockenleistung zu erzielen. Alle Luft- und Dampfeinschlüsse im Produkt werden abgeführt und die Rückkondensation nach dem Trocknungsprozess wird zuverlässig verhindert. Das macht die Vakuumtrocknung überall dort zur perfekten Lösung, wo Feuchtigkeit schonend, rückstandslos und prozesssicher aus empfindlichen Materialien entfernt werden muss.
Wie kann die Vakuumtrocknung bei der Batteriefertigung eingesetzt werden?
Vakuumtrocknung ist der finale Schritt in der Elektrodenfertigung. Damit die Batterien später sicher die geforderte Performance und Langlebigkeit bieten, müssen die beschichteten Coils bestmöglich getrocknet werden. Dabei werden ihnen auch kleinste Rückstände an Feuchtigkeit und Lösemittel entzogen. Vakuumtrockner mit Umluft-Temperierung realisieren diesen Prozess besonders effizient. Nach dem vollständigen Trocknen werden die Coils zur Zellassemblierung überführt, wo sie unter kontrollierten Trockenraumbedingungen – beispielsweise Taupunkt - 60°C - weiterverarbeitet werden.
Wie optimiert Vakuumtrocknung die Fertigung von Lithium-Ionen-Batterien?
Derzeit gibt es noch keine etablierten oder normierten Standardprozesse für die Vakuumtrocknung bei der Batteriefertigung. Deshalb ist es spannend, Forschungsfertigungen zu begleiten und zu helfen, diese Standards zu entwickeln. Wir tun dies mit unseren kundenspezifischen und prozessoptimierten Lösungen zur Vakuumtrocknung für die effiziente und sichere Batteriefertigung. Diese binden wir bedarfsgerecht in die Produktionslinie ein. Da in der Elektrodenfertigung brennbare Lösemittel eingesetzt werden, ist die Prozesssicherheit ein besonders wichtiger Aspekt. Um diese zu gewährleisten, nutzen wir unsere tiefgehende Erfahrung in der Wärmetechnik.
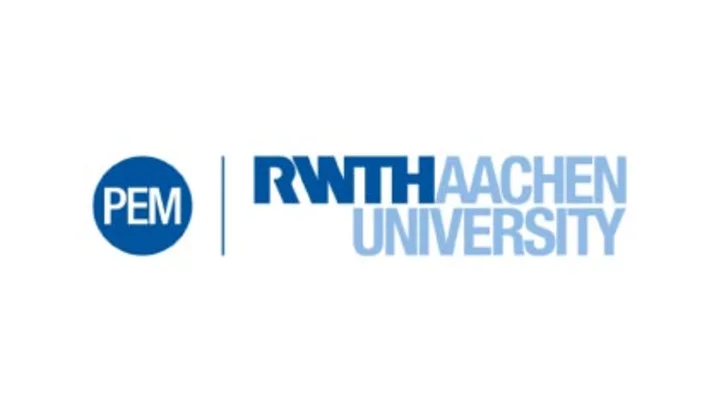
Solid-state Batterie – Speichertechnologie mit Herausforderungen in der Produktion
Solid-State Batterien gelten als Zukunftstechnologie. Im Vergleich zu herkömmlichen Lithium-Ionen-Batterien bieten sie zahlreiche Vorteile. Sie ermöglichen größere Reichweiten und schnellere Ladezeiten für Elektrofahrzeuge, was sie besonders für die Automobilindustrie attraktiv macht. Ein zusätzlicher entscheidender Vorteil ist die erhöhte Sicherheit: SSBs verwenden nicht entflammbare Festelektrolyte, die das Risiko von Bränden und Explosionen erheblich reduzieren und somit den hohen Sicherheitsstandards für Elektrofahrzeuge gerecht werden.
Die Heat Technology hat sich gemeinsam mit weiteren Industrieteilnehmern einer Konsortialstudie mit den produktionstechnischen Herausforderungen von Solid-state-Batterien befasst. Unter der Federführung des PEM der RWTH Aachen wurden in Workshops die Herausforderungen der unterschiedlichen Technologien rund um die (All-) Solid-State Batterie ((A)SSB) untersucht.
Die aktuellen Entwicklungen zeigen drei vielversprechende Technologien für SSBs: Polymer-, Sulfid- und Oxid-basierte SSBs. Jede dieser Technologien bringt ihre eigenen Vor- und Nachteile mit.
Polymer basierte SSBs sind bereits in kommerziellen Bussen im Einsatz. Jedoch gibt es noch Einschränkungen hinsichtlich der Energiekapazität und Lebensdauer, was ihre Anwendung in Personenkraftwagen derzeit limitiert. Der erste kommerzielle Einsatz von Polymer-SSBs zeigt jedoch deutlich das Potenzial für eine breitere Anwendung, sofern Weiterentwicklungen vorgenommen werden, um den Anforderungen von Personenkraftwagen gerecht zu werden.
Sulfid basierte SSBs verfügen über vielversprechende Eigenschaften, stehen aber vor Herausforderungen in der Massenproduktion. Hohe Kosten und Qualitätskontrollprobleme, insbesondere bei den Elektrolyten, erschweren die großflächige Anwendung.
Oxid basierte SSBs zeigen ähnlich/vergleichbar großes Potenzial, kämpfen jedoch ebenfalls mit hohen Produktionskosten und Qualitätsproblemen.
Die Produktion von SSBs umfasst mehrere komplexe Schritte, die je nach Elektrolyt Technologie variieren. Wie diese im Detail aussehen können, wurde im Rahmen der Studie erarbeitet. Für Polymer SSBs, Sulfide SSBs und Oxide SSBs müssen spezifische Produktionsprozesse entwickelt und optimiert werden, um die Effizienz und Qualität zu maximieren. Dies beinhaltet die Synthese und Verarbeitung der Festelektrolyte, die Integration der Elektroden und die Montage der Batteriezellen.
Die Konsortialstudie des PEM der RWTH Aachen zeigt, dass Solid-State Batterien ein enormes Potenzial für die Zukunft der Elektromobilität bieten. Trotz der bestehenden Herausforderungen in der Produktion, insbesondere hinsichtlich der Kosten und Qualitätskontrolle, sind die Fortschritte vielversprechend. Mit weiteren Entwicklungen und Optimierungen könnten SSBs schon bald eine Schlüsselrolle in der Automobilindustrie spielen und die Elektromobilität auf ein neues Niveau heben.

Innovative Batteriezellenfertigung
Weiss Technik Heat Technology liefert Vakuumtrocknungsanlage für Fraunhofer-Einrichtung Forschungsfertigung Batteriezelle FFB
Fortschreitender Klimawandel und zur Neige gehende fossile Brennstoffe steigern die Nachfrage nach alternativen Energieträgern für Elektrofahrzeuge, PV-Anlagen sowie andere private und gewerbliche Anwendungen. Die Batteriezellenfertigung wird so zur Schlüsseltechnologie für die Energie- und Mobilitätswende.
Eine ökologische und ökonomische Batteriezellenfertigung in der Großserie ist in Deutschland derzeit noch im Aufbau. Um zu erforschen, wie die Fertigung von Lithium-Ionen-Batterien optimiert werden kann, baut deshalb die Fraunhofer-Gesellschaft gemeinsam mit ihren Standortpartnern die Fraunhofer-Einrichtung Forschungsfertigung Batteriezelle FFB (Fraunhofer FFB) in Münster auf. Die Erfahrungen aus dieser Forschungsfertigung sollen Unternehmen befähigen, ihre eigenen Produktionstechnologien schneller und effizienter weiterzuentwickeln.
Lithium-Ionen-Batterien und andere nachhaltige Energiespeicher sind während der Herstellung sehr temperatursensibel. Deshalb werden sie nicht nur in Trockenräumen produziert, sondern zusätzlich in Vakuumtrocknern nachgetrocknet. So wird die Restfeuchte auf ein Minimum reduziert und somit die Produktqualität und -zuverlässigkeit sichergestellt. Unser Geschäftsbereich Heat Technology konnte sich in einem internationalen Ausschreibungsverfahren durchsetzen und entwickelt und liefert für die Ausbaustufe Gigafab der FFB Fab in Münster die entsprechende Vakuumtrocknungsanlage mit Abluftbehandlung zum Nachtrocknen von Elektroden-Coils.
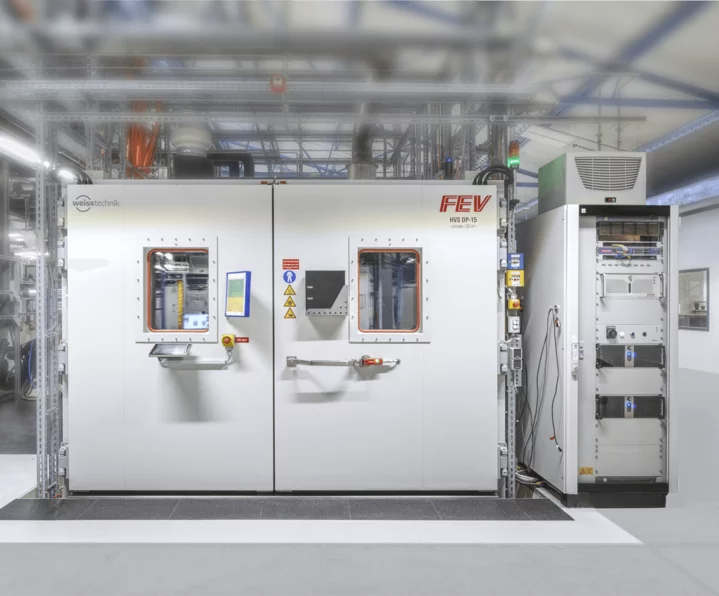
Schneller sicher trocknen
Prozesszeiten optimieren
Bei der industriellen Batteriefertigung sind kurze Prozesszeiten wichtig. Um die temperatursensiblen Batterieelektroden möglichst schnell und gleichzeitig vollständig und sicher zu entfeuchten, empfehlen wir besonders schonende Hybrid-Trockensysteme mit Umlufttemperierung. Der schnelle Prozess mit kurzer Anheizzeit erzielt optimale Trockenergebnisse und eliminiert Lufteinschlüsse in den Elektroden. Dies ist entscheidend für die Leistungsfähigkeit der Batterien.
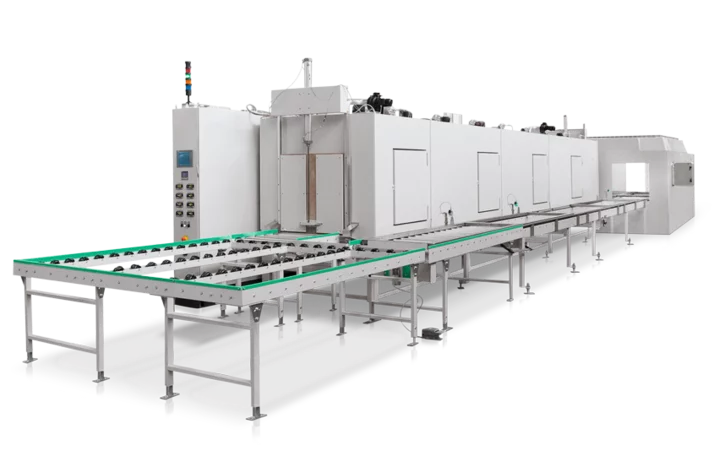
Flexible Integration in Forschung und Produktion
Maßgeschneiderte Batch- und Durchlauföfen
Je nach Anwendung und Prozess entwickeln wir Vakuumtrocknungslösungen, die sich nahtlos in die Batterie-Fertigungslinie einfügen: kundenspezifische Batchöfen mit maßgeschneiderten Coilaufnahmen oder in Fertigungsstraßen integrierte Durchlauföfen für hohe Produktionskapazitäten. Unsere Vakuumtrocknern eignen sich sowohl für Forschungsprojekte als auch für die industrielle Batteriefertigung.
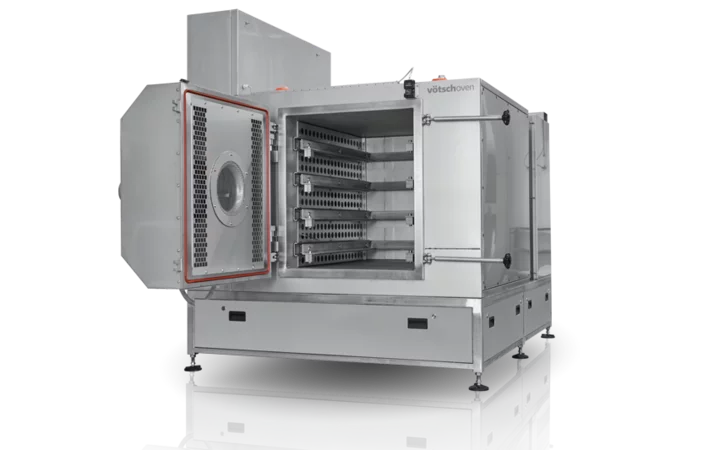
Immer alles unter Kontrolle
Sichere Qualität durch konstante Fertigungsbedingungen
Für eine hohe Batteriequalität muss die gesamte Fertigung unter kontrollierten, trockenen Umgebungsbedingungen ablaufen. Ein entscheidender Punkt ist dabei die Verbindung zwischen den einzelnen Fertigungsschritten. Vakuumtrockner können als Schleuse für die Elektroden zwischen den verschiedenen Trockenräumen genutzt werden. Das Durchführen der Coils durch die Schleuse stellt dabei sicher, dass die niedrigen Taupunkte von -40 bis -60 ºC nicht unterbrochen werden.
Alles aus einer Hand
Lösungen für die Fertigung von Lithium-Ionen-Batterien
Als Teil der Schunk Group bieten wir Erfahrung, Kompetenz und vielfältige Lösungen für die Fertigung von Lithium-Ionen-Batterien. Dazu gehören unter anderem innovative und flexibel einsetzbare Ultraschallschweißlösungen von Schunk Sonosystems, Adsorptionstrockner von Weiss Klimatechnik für zuverlässig niedrige Taupunkte und unterschiedlichste Umweltsimulationslösungen, um Batterien unter verschiedensten Bedingungen zu testen.