We offer fully automated equipment and system solutions for applications in clean and dry rooms, all perfectly coordinated in terms of control technology.
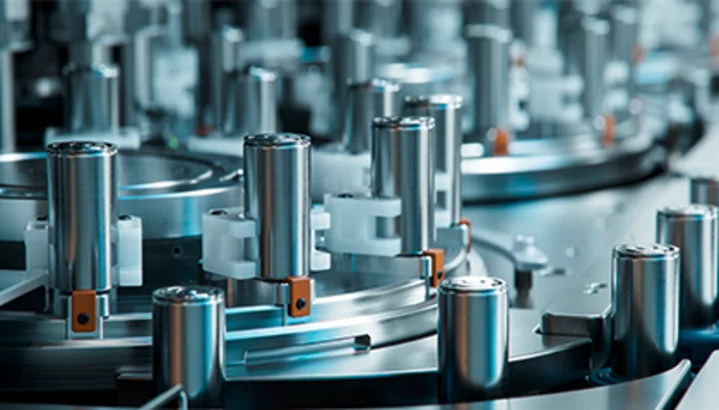
Innovative air management: the future of battery cell production
Battery cell production requires clean and extremely dry air in order to process moisture-sensitive materials such as nickel and lithium into powerful, long-lasting battery cells. The dry ambient air has so far been provided in large clean and dry rooms with correspondingly large air volumes. This highly energy-intensive process requires up to 50% of the total energy demand for battery cell production.
As part of the QueEn project, Weiss Klimatechnik is taking a completely new approach to making battery cell production more efficient, reducing costs, and ensuring product quality: innovative air management in mini-environments.
Dry air with extremely low dew points
The required dry air for battery cell production has extremely low dew points, currently at -40 °C. New materials for cathodes and electrolytes are even more moisture-sensitive and require dew points as low as -60 °C or lower. This further increases the already high energy demand for air drying.
Protecting Personnel, Preventing Contamination
The dry air in clean and dry rooms poses a significant physical strain on operating personnel. Operators are also one of the biggest sources of contamination. Depending on their level of activity, they introduce particles and a moisture load of 90 to 120 g/h into the process.
Securely Controlling Processes
The high-precision monitoring of temperature, humidity, particle size, and quantity is essential to ensuring the optimal functionality of battery cells. Increasing demands on product quality and lifespan also raise the requirements for air regulation and process security.
Ensuring Long-Term Economic Viability
Battery cell manufacturers must take action: The current energy-intensive production process is not economically viable and presents enormous challenges for industrial locations in Germany and Europe. Significantly reducing the energy costs of air drying provides an excellent opportunity to make a lasting improvement in economic efficiency.
- Battery cell manufacturers
- Process equipment manufacturers
- Research institutes and laboratories
- Automotive manufacturers and suppliers
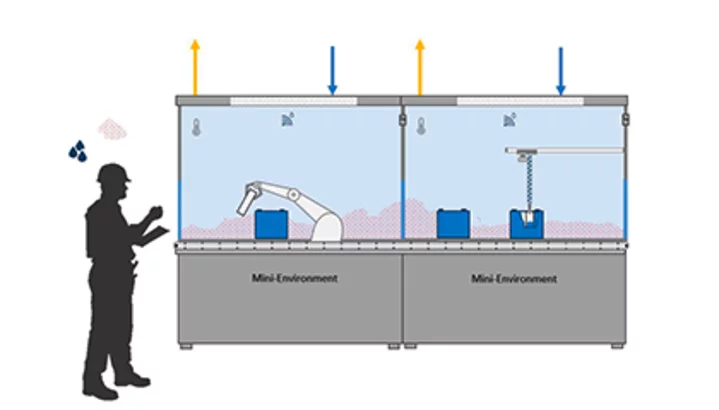
Mini-Environments replace large dry rooms
Process-oriented mini-environments featuring innovative air management represent a significant advancement in battery cell production. These mini-environments serve as encapsulated production areas, creating compact, enclosed, and controlled spaces for critical processes. They allow for the precise regulation of air, ensuring it meets the necessary levels of dryness and cleanliness. As a result, only moderate climate conditions are needed in the surrounding production hall to ensure safe manufacturing processes.
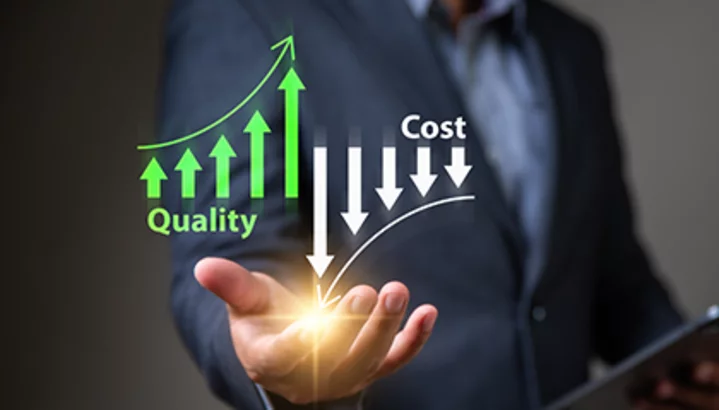
Benefits of Mini-Environments with Innovative Air Management
-
Up to 80% lower energy consumption and costs
-
Reduced CO2 footprint
-
Precise dew point control at the point of use
-
Higher product quality due to stable dew point conditions
-
No moisture ingress caused by personnel
-
Optimized protection of personnel, product, and process
Deep Dive into Mini-Environments by Weiss Klimatechnik
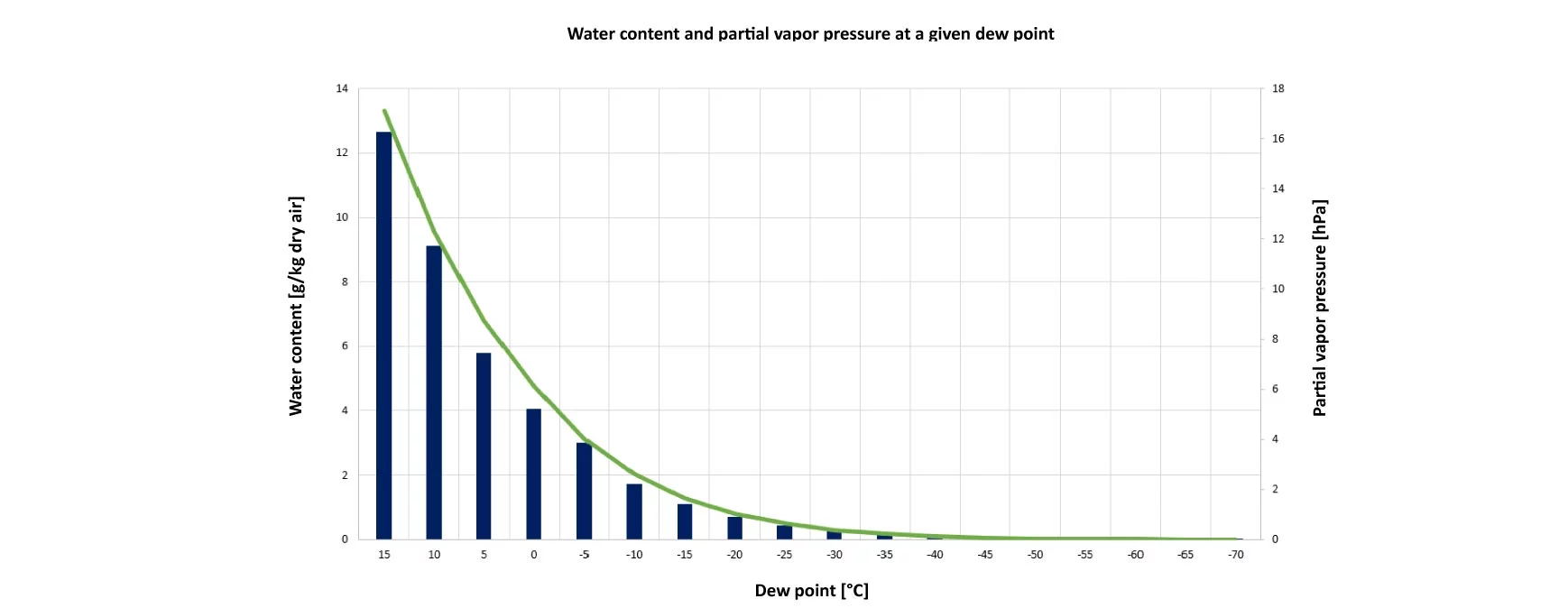
At an ambient temperature of 20°C and a dew point of -60 °C, this corresponds to a partial vapour pressure of 0.011 hPa. The water content is only 0.007 g/kg of dry air.
The dew point describes the point at which moisture condenses in the air
Green curve I Partial vapour pressure
Blue bars I Values for the water content per kilogramme of dry air
At an ambient temperature of 20°C and a dew point of 17°C, this corresponds to a partial vapour pressure of 17 hPa. The water content is 12 g/kg of dry air.
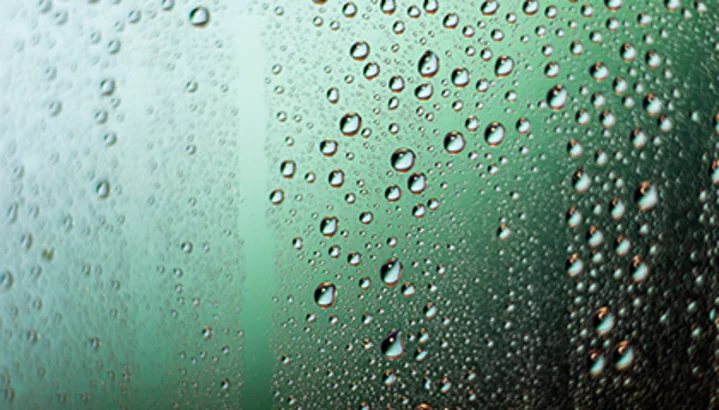
Innovative air management ensures constant climate parameters
Maintaining climate parameters is essential for ensuring consistent process quality in battery cell production. In this context, dry air plays a crucial role as a guiding factor. This is achieved through a stable and consistent dew point, which we maintain with our innovative air management system.
It is important to note that the water content in the air at a dew point of -60 °C is approximately 1,700 times lower than that at a dew point of 17 °C. Moreover, the partial vapor pressure is significantly decreased, which makes process control more challenging. The air supply volume flow presents both energy and cost challenges, as it increases exponentially when the dew point decreases. We address these complex requirements by utilizing innovative approaches in system design, material selection, sensors, and control and regulation technology.
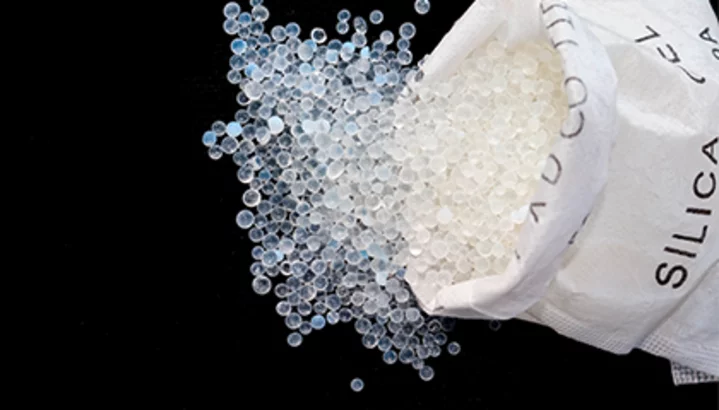
Adsorption drying ensures extremely low dew points
Conventional wet dehumidification (condensation) is inadequate for the extremely low dew points required in battery cell production. Instead, we utilize specially developed adsorption dryers to reach the required dew points.
This process chemically binds water to a highly hygroscopic drying material, typically silica gel. The air being dried passes through a large, porous surface of this drying material, which effectively dehumidifies the air to the desired dew point temperature. In a counterflow configuration, the absorbed moisture is expelled using hot regeneration air. This approach enables the implementation and precise control of a continuous dehumidification process, achieving dew point temperatures as low as -70 °C and even lower.
Energy-efficient, Economical, Sustainable
Interested in a Mini-Environment Solution for Your Battery Cell Production?
Our innovative mini-environments have reliably demonstrated their effectiveness in the proof-of-concept phase. Our experts are available to discuss a customized solution for your production needs or the possibility of developing a research or pilot plant for you.
Contact us!